L'industria 5.0 oltre la teoria: i passi da fare e gli strumenti che ti servono
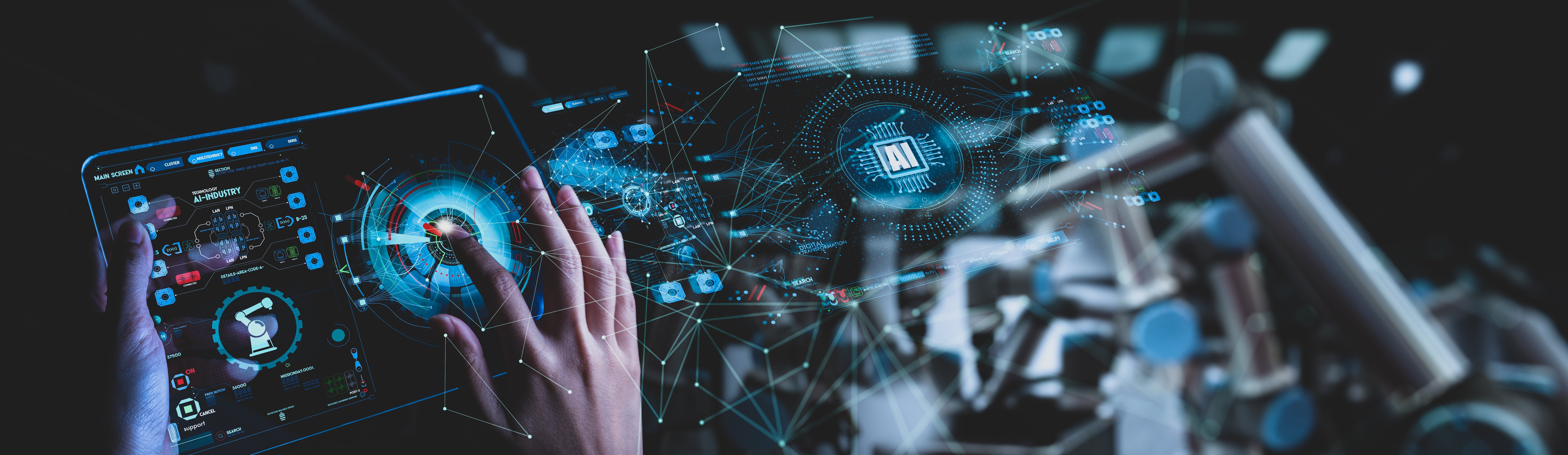
Da diversi anni, il paradigma Industria 5.0 suscita interesse e dibattito. Per comprenderne l’essenza, è fondamentale riconoscere che esso evolve dal modello 4.0 e che, partendo dai suoi benefici di efficienza, innovazione e produttività, ambisce a una visione più ampia, incentrata sulla sostenibilità e sulla centralità dell’uomo. Alla base del nuovo paradigma, infatti, c’è il riconoscimento del ruolo dell’industria rispetto ai grandi temi globali come il cambiamento climatico, la sostenibilità ambientale e il benessere sociale.
Il punto di partenza è sempre industria 4.0
A proposito di Industria 5.0 e dei concetti gemelli di fabbrica sostenibile e fabbrica resiliente, c’è molta letteratura in merito, tra documenti governativi, pubblicazioni della Commissione Europea e svariati approfondimenti sui principi, le motivazioni e i potenziali benefici a livello sistemico.
Se invece rivolgiamo l’attenzione all’implementazione pratica, applicare in azienda i principi 5.0 potrebbe non essere banale poiché, a differenza dei modelli precedenti, qui non si tratta di integrare tecnologia avanzata, ma di rivedere processi, strategie, tecnologie, organizzazione e cultura verso scopi più ampi (e nobili) della sola produttività, dell’efficienza e dell’automazione.
Resta il fatto che la prima cosa da fare sia valutare lo stato dell’arte dell’azienda in ottica 4.0. Come detto, 4.0 è il pilastro su cui si costruisce la fabbrica sostenibile, resiliente e human-centric, e di per sé l’impiego di tecnologie 4.0 va nella direzione giusta perché abbatte gli sprechi e gli errori, ottimizza i processi, permette di impiegare in modo più efficiente le risorse e di allungare il ciclo di vita dei prodotti. Adottare un modello 4.0 è dunque un passo avanti non solo nei confronti della sostenibilità ambientale, ma anche un avanzamento verso un modello economico circolare.
Industria 5.0 e la fabbrica sostenibile: come fare
Non ci si può aspettare, però, che il modello 5.0 sia la conseguenza diretta di scelte indirizzate verso scopi diversi dalla sostenibilità e dalla centralizzazione della persona. La sostenibilità deve essere un vero e proprio obiettivo aziendale e deve plasmare le decisioni a tutti i livelli; la trasformazione green, in altri termini, deve correre parallelamente a quella digitale: non a caso, si parla di transizioni gemelle, o twin transitions.
Da un’azienda impegnata nel percorso 5.0 ci si aspetta l’impiego di fonti di energia rinnovabile, di soluzioni che ottimizzino l’uso di risorse idriche ed energetiche, la trasformazione dei processi in ottica circolare, l’adozione di una politica “zero waste” e molto altro. Tutti questi requisiti impongono l’uso di tecnologie avanzate (4.0), tra cui:
- L’intelligenza artificiale, in una delle sue molteplici declinazioni, può per esempio identificare pattern che consentono di ridurre i consumi energetici attraverso la previsione della domanda.
- I sensori IoT sono fondamentali per monitorare i consumi di energia e acqua, segnalando eventuali anomalie o inefficienze e permettendo di prendere decisioni tempestive.
- I digital twin consentono di simulare e ottimizzare le operazioni senza dover intervenire direttamente sulla produzione. Questo approccio permette anche di identificare miglioramenti e soluzioni per ottimizzare l'uso delle risorse.
L’evoluzione verso la fabbrica human-centric
Quanto sopra può fornire alle aziende qualche spunto nell’ottica di una trasformazione green che, comunque, non può prescindere da un’evoluzione culturale più o meno profonda a seconda del punto di partenza. Ma che dire della componente sociale e human del paradigma 5.0?
Anche in questo caso, bisogna immediatamente riconoscere che la visione della smart factory (4.0) non è per nulla in contrasto con la centralità dell’uomo. Occorre semplicemente adottarla nel modo corretto, ad esempio attraverso percorsi di formazione e riqualificazione, che sono fondamentali per l’integrazione delle persone in contesti sempre più automatizzati, ma anche valorizzando al massimo le competenze umane che non possono essere replicate da macchine o algoritmi.
Inoltre, è fondamentale implementare politiche aziendali che favoriscano un ambiente di lavoro inclusivo e sicuro, dove la tecnologia supporti le capacità umane. Non è un caso che i cobot, o robot collaborativi, siano una tecnologia chiave di industria 5.0, il cui fine è migliorare la sicurezza sul posto di lavoro e aumentare l'efficienza nelle operazioni.
Anche la fabbrica resiliente è un pilastro di Industria 5.0 e richiede valutazioni approfondite sia sulla resilienza dei processi interni che su quella, più complessa, della supply chain. Il tema, ovviamente, è diventato centrale a causa degli eventi degli ultimi anni, dal covid alle tensioni geopolitiche, e richiede senz’altro un approccio sistemico, che spazi dalla capacità (di ogni azienda) di identificare e mitigare le vulnerabilità delle supply chain fino allo sviluppo di modelli decentralizzati e nativamente resilienti.