3 modi per trasformare la fabbrica 4.0 con i Digital Twin
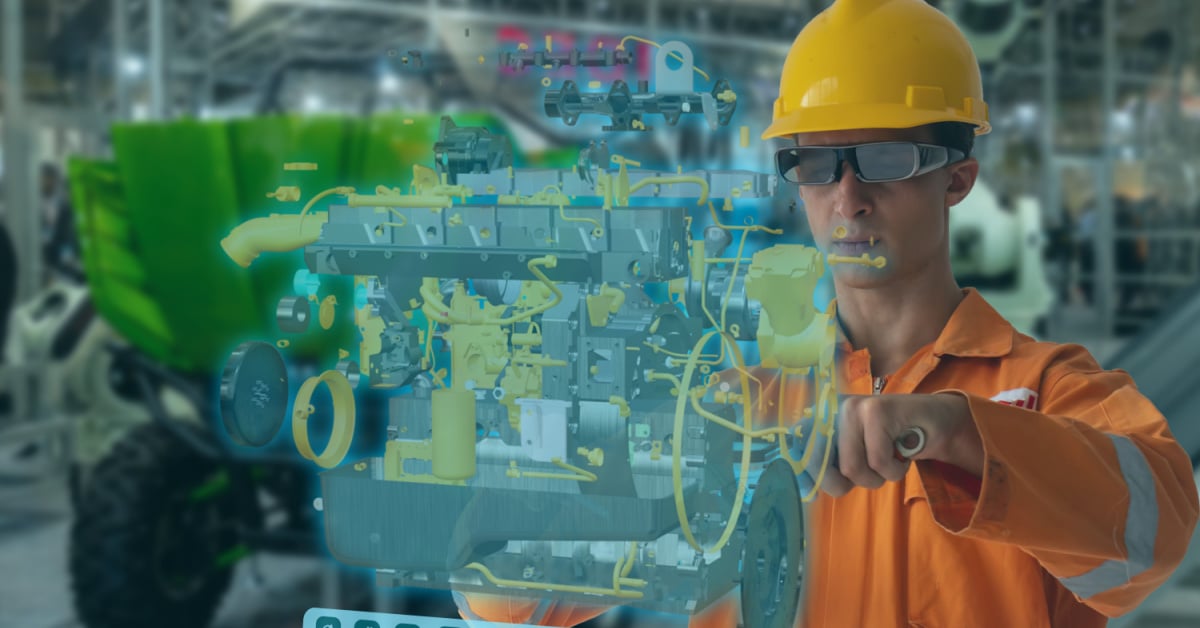
Il digital twin si sta affermando come una delle tecnologie chiave della fabbrica 4.0, grazie alla sua capacità di creare nuovi scenari per l’industria manifatturiera, e non solo, sempre più tesa verso soluzioni innovative in grado di migliorare la produttività. Un recente studio di Straits research rivela che circa il 75% delle aziende globali che già utilizzano o stanno iniziando ad utilizzare l‘Internet of things fa uso di digital twin o ha in programma di farlo entro i prossimi 12 mesi. I dati confermano questa tendenza. Secondo gli analisti della società di ricerca, infatti, il mercato mondiale dei digital twin, valutato su scala mondiale 9,7 miliardi di dollari nel 2022, raggiungerà 185,78 miliardi di dollari entro il 2031, crescendo a un Cagr del 38,8% durante nel periodo 2023–2031. Il segmento automobilistico e dei trasporti ha la quota di mercato più alta, con una previsione di crescita a un Cagr del 39,2% nello stesso periodo. Non è difficile immaginare come i digital twin, che incorporano Big Data, Intelligenza Artificiale, Machine Learning e Internet of Things, guideranno l’innovazione tecnologica verso la fabbrica 4.0 per il prossimo decennio, aprendo nuovi scenari di business nell’industria grazie alla capacità di ampliare le possibilità della simulazione e della prototipazione.
Che cosa sono i digital twin
Il gemello digitale è una replica virtuale dinamica di un sistema fisico, sia esso un prodotto, un processo o un ambiente che, sfruttando l’intelligenza artificiale, l’Internet of Things (IoT) e l’analisi dei dati, riproduce in modo fedele il comportamento effettivo della sua controparte reale in varie condizioni. Si tratta dunque di un modello tridimensionale di tutti gli aspetti dell’oggetto fisico, a livello meccanico, geometrico e elettronico, in grado di interagire con l’ambiente circostante in modo realistico. Per realizzare un gemello digitale sono necessari tre elementi: un prodotto fisico nello spazio reale, un suo gemello digitale nello spazio virtuale e un sistema di collegamento per il flusso delle informazioni tra spazio fisico e virtuale.
L’integrazione dei digital twin nella fabbrica 4.0 consente attività di diagnosi, ottimizzazione e predizione accurate su impianti, sistemi, processi, dispositivi, prodotti e componenti. L’analisi dei dati e il monitoraggio dei sistemi in tempo reale lungo l’intero ciclo di vita del prodotto/impianto, permette inoltre di identificare rapidamente le inefficienze e apportare modifiche al processo produttivo, incrementandone l’efficienza e la sostenibilità. Ogni dato costituisce un “engineering item”, cioè un “oggetto” esplorabile, confrontabile, tracciabile e utilizzabile per prendere decisioni.
Il Virtual design e lo sviluppo nuovo prodotto
Grazie alla possibilità di testare e capire in un ambiente virtuale come sistemi e prodotti da realizzare si comporteranno in un’ampia varietà di contesti, simulando diverse strategie di produzione, i digital twin abilitano il virtual design e lo sviluppo di nuovi prodotti, permettendo di ridurre in modo significativo i tempi di elaborazione modifiche e manutenzione di prodotto e i costi correlati e di minimizzare gli sprechi. A questo proposito, presso il MADE Competence Center, le aziende possono sperimentare le metodologie e gli strumenti più innovativi per lo sviluppo digitale di nuovi prodotti toccando con mano, nei vari dimostratori presenti, le tecnologie che permettono la completa digitalizzazione dei dati a supporto del processo: dal PLM (Product Lifecycle Management) per la gestione dei dati del prodotto al software CAD (Computer-Aided Design) per la progettazione assistita da computer e agli strumenti di simulazione avanzata dei digital twin, sperimentando la visualizzazione dei risultati delle simulazioni effettuate direttamente in ambienti di realtà virtuale immersiva (virtual room), interattivi e collaborativi, integrati con la realtà virtuale e aumentata.
3 modi per trasformare la fabbrica 4.0
Oggi, in contesti industriali che operano in mercati caratterizzati da incertezza e volatilità della domanda, riuscire a creare digital twin degli asset aziendali permette di superare le sfide di progettazione, fabbricazione e consegna degli stessi ai clienti, analizzando a fondo le caratteristiche del processo produttivo e del prodotto, prevenendo errori di progettazione e prevedendo le performance finali. Integrati nella realtà aumentata (AR), i digital twin sono utilizzati in vari settori industriali e funzioni aziendali, nella formazione (virtual training) degli operatori addetti ai macchinari, nei processi di progettazione, nella gestione e controllo degli impianti di produzione ad alta automazione, fino al marketing e alla manutenzione del prodotto tramite assistenza remota.
Le potenzialità dei digital twin di trasformazione della fabbrica 4.0 sono distribuite su 3 differenti livelli, da una visione olistica alla visione puntuale della singola stazione di lavoro:
- a livello di sistema operations: il digital twin viene utilizzato per prevedere le prestazioni della fabbrica vista come sistema complesso di interazione di molteplici asset, portando vantaggi a tutti i livelli delle operazioni di produzione. Grazie al mapping delle fabbriche, è possibile ottimizzare i layout delle macchine, i flussi di assemblaggio, le interazioni dei dipendenti. Con i digital twin basati sui processi, le aziende ottengono visibilità sulla produzione e sulla relativa pianificazione, aumentando l'agilità operativa e il throughput e ottimizzando l'efficienza dei processi per l'intera supply chain. Il gemello digitale, quindi, supporta analisi di costi e performance, pianificazione e controllo, valutazione dei colli di bottiglia, valutazioni di investimenti.
- a livello di macchina (virtual commissioning): grazie al gemello digitale della macchina si possono prevenire errori di progettazione senza dover testare sul campo. Interfacciando il modello digitale con il controllore fisico (PLC, Programmable Logic Controller) o con il suo digital twin, è possibile implementare e collaudare il software di controllo prima che il macchinario venga assemblato e messo in funzione. Il Digital Twin della macchina integra automazione e meccanica, per una qualità in fase avviamento più elevata.
Attraverso una progettazione tecnica a loop chiuso, vengono ottimizzate la forma, l'aspetto e la funzione del prodotto, come anche la qualità, compresa quella dei collaudi, convalidando le prestazioni prima dell’uso sul campo al posto dei prototipi fisici, riducendo la costosa riprogettazione in fasi successive e accelerando il time-to-market con cui riesce a consegnare la macchina/il prodotto all’utente finale. Integrando il virtual commissioning con tecniche di data science e di elaborazione di modelli previsionali, si può potenziare il supporto dei processi di post-vendita e contribuire a un continuo miglioramento del prodotto. Il Virtual Commissioning quindi non è soltanto una simulazione meccanica o visuale del comportamento del prodotto, della macchina o del processo, è molto di più.
- a livello di postazione di lavoro manuale: il digital twin replica le condizioni di lavoro della postazione manuale e simula le attività svolte dall’operatore. In questo modo può calcolare il rispetto dei parametri di sicurezza ed ergonomia, nonché trovare la configurazione delle attività e della postazione che ottimizza sforzi e produttività.
I vantaggi che ne derivano sono molteplici: le aziende migliorano l'agilità e la resilienza della catena di approvvigionamento, avendo completa visibilità della loro catena di fornitura, riducono il time to market dei prodotti, grazie alle continue informazioni sulle prestazioni dei loro prodotti sul campo fornite dai digital twin, abilitano nuovi modelli di business, connessi ad una maggiore visibilità dei dati dei prodotti e, ad esempio, alla possibilità di considerare il prodotto come servizio. Vengono inoltre, migliorate la qualità dei prodotti, l’efficienza operativa e la produttività, identificate opportunità di sviluppo sostenibile lungo tutta la catena del valore (sostituzione dei materiali dei prodotti con opzioni più sostenibili, riduzione delle emissioni di carbonio o dei rifiuti nel processo di produzione, ecc.) e aumentata la soddisfazione dei clienti, sia attraverso la manutenzione predittiva che le informazioni sui futuri miglioramenti del prodotto.