Come mettere in pratica concretamente il Lean Manufacturing
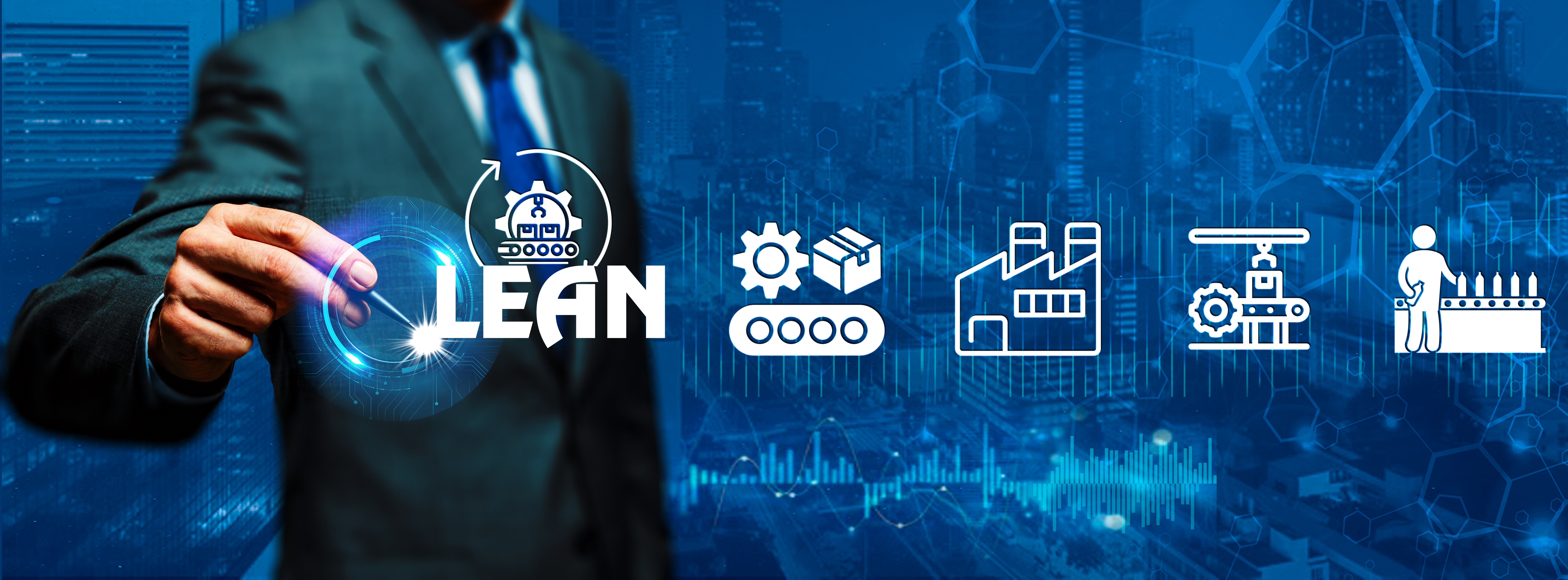
L'industria moderna affronta quotidianamente una serie di sfide che non si esauriscono nell’intensa competizione globale, nell'instabilità dei costi delle materie prime e nella necessità di garantire la resilienza delle catene di approvvigionamento. Gli operatori, infatti, provano anche una forte esigenza di sostenibilità e di efficienza, senza le quali non sarebbero in grado di rispondere alle mutevoli richieste dei mercati, che sempre più spesso chiedono personalizzazione e time to market ridotto. Questi fattori spingono le imprese a innovare continuamente e ad adottare approcci metodologici con cui ottimizzare i processi produttivi, anche (e soprattutto) con l’ausilio della tecnologia. Questo è il terreno in cui si muove il Lean Manufacturing.
Lean Manufacturing: prima la teoria
Da manuale, Lean Manufacturing è un sistema o un metodo di gestione della produzione il cui fine è generare il massimo valore per il cliente riducendo al minimo gli sprechi.
I due concetti chiave, entrambi riconducibili alla cultura giapponese (laddove il metodo nacque alla metà del secolo scorso), sono quindi:
- l’abbattimento dello spreco, stella polare per l’analisi, la configurazione e la riconfigurazione del flusso produttivo (perdite di processo, tempi morti dovuti all’attrezzaggio delle macchine, difettosità…);
- la centralità del cliente, del quale il produttore deve comprendere le esigenze e capire come soddisfarle.
Lean manufacturing non ragiona in ottica push, ovvero investendo massicciamente sulla creazione di una domanda tale da giustificare la produzione di massa, bensì pull, cioè nel creare valore per il cliente e far sì che esso sia naturalmente attratto dal prodotto. Risulta a questo punto evidente perché il lean manufacturing sia la scelta ideale per i mercati moderni, dove le esigenze dei consumatori cambiano di continuo e la creazione del valore non può prescindere da un certo grado di personalizzazione, che dipende dalla flessibilità di tutto il processo produttivo a monte.
Dalla teoria alla pratica, i pilastri dell’approccio lean
Se Lean Manufacturing è un approccio, una filosofia gestionale, in che modo la si concretizza, realizzando i suoi obiettivi di generazione del valore e di abbattimento degli sprechi?
Per prima cosa, occorre adottare un metodo di produzione adeguato alla filosofia lean. Il Just in Time (JIT), basandosi nativamente su una logica pull che adegua la produzione all’effettiva domanda di mercato, è il candidato per eccellenza.
Per operare in ottica lean, è poi fondamentale poter procedere con la cosiddetta mappatura del flusso di valore (Value Stream Mapping, o VSM), una sorta di assessment evoluto con cui descrivere, tramite dati certi, tutto il percorso del prodotto, dalla materia prima al cliente. A patto di poter contare su tanti dati di qualità, VSM è uno strumento eccellente per identificare gli sprechi, riportandoli agli otto tipi della metodologia lean, e soprattutto per rivedere i processi in ottica di ottimizzazione dell’efficienza e della flessibilità.
Molti altri processi, tool e strumenti aiutano le aziende ad adottare i principi lean, tra cui:
- la metodologia SMED (Single Minute Exchange of Die) per la riduzione dei tempi di attrezzaggio delle macchine, che ancora oggi rappresentano una importante voce di spreco;
- la logica Kaizen, che ha plasmato il concetto di miglioramento continuo e che si sostanzia in una continua ricerca della perfezione (essenza del lean thinking);
- l’implementazione delle 5S per l’organizzazione delle aree produttive.
Il contributo della tecnologia nel lean manufacturing
Operare in ottica di lean manufacturing comporta, per molte realtà, un processo di trasformazione significativo. Ma qual è, in tutto questo, il ruolo della tecnologia?
Semplificando, il rapporto tra lean manufacturing e tecnologia 4.0 è sinergico, essendo quest’ultima centrale in chiave di efficienza e di miglioramento continuo. Essa si integra perfettamente con i principi cardine del lean, amplificando i suoi benefici e aprendo nuove frontiere di ottimizzazione.
In particolare, la trasformazione lean conduce a una revisione dei processi nell’ottica della massima generazione di valore e della lotta agli sprechi. Riorganizzando e ottimizzando i flussi e i cicli di lavoro, l’azienda ha la certezza di perseguire l’eccellenza operativa e di non sprecare budget digitalizzando gli sprechi. Le soluzioni digitali, che a questo punto vengono introdotte in un contesto ottimizzato, possono concretizzare, e in taluni casi amplificare, gli effetti della metodologia lean, realizzandone tutto il potenziale.