Efficienza di produzione: migliorarla con 5 tecnologie emergenti
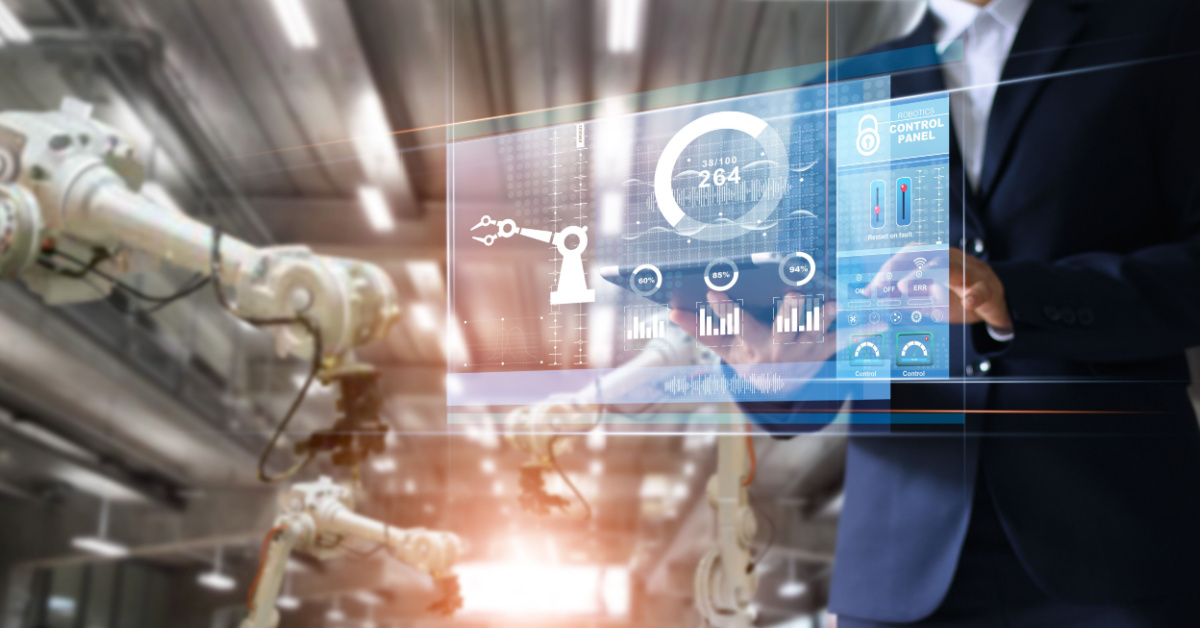
Per le Smart Factory migliorare l'efficienza di produzione è essenziale per rimanere competitive in un contesto industriale in continua evoluzione e per affrontare con successo le molte sfide per adeguarsi ai cambiamenti. In tema di “Green e Digital Transition”, che rappresentano due capisaldi dell'Europa del futuro, le imprese, piccole, medie e grandi, sono dunque chiamate a compiere passi importanti per cambiare il modo in cui operano, producono e innovano. La transizione verde e digitale è guidata da alcune tecnologie emergenti, la cui adozione, quindi, aiuterà l’industria manifatturiera a diventare più competitiva, digitale, verde e resiliente. Le tecnologie digitali, alla base del nuovo modello di produzione Industria 4.0, includono l’Internet of Things, l’Intelligenza Artificiale, il Digital Twin, la Robotica e la Logistica 4.0. Possono essere considerate tecnologie emergenti per come stanno rivoluzionando il modo in cui le aziende producono e distribuiscono i loro prodotti, aprendo la strada a un futuro più efficiente e automatizzato. Tuttavia, digitalizzare la propria impresa per aumentare la competitività non è sufficiente. È infatti cruciale per l’impresa adottare un approccio strategico in cui le tecnologie digitali sono integrate con una visione Lean dei processi logistici e produttivi, con la quale creare una base su cui introdurre le infrastrutture tecnologiche. I molti vantaggi derivanti dall’adozione di tecnologie emergenti per il settore manifatturiero consistono nella loro capacità di sbloccare nuovi modelli di business, adattarsi più rapidamente ai cambiamenti e anticiparli prima che si verifichino.
L’impatto delle tecnologie emergenti sulla produzione
L’adozione delle tecnologie IoT (IoT devices) rende la produzione industriale sempre più automatizzata e connessa. È sempre più diffuso tra le aziende l’utilizzo di sensori e dispositivi IoT per monitorare e gestire i processi produttivi in tempo reale, consentendo di ottimizzare la loro efficienza e ridurre i costi. Secondo il report di IoT Analytics "State of IoT—Spring 2023", nel 2022 il numero di connessioni IoT globali ha raggiunto i 14,3 miliardi di endpoint IoT attivi, con una crescita del 18%. Nel 2023, si prevede che il numero globale di dispositivi IoT connessi crescerà di un altro 16%, con 16,7 miliardi di endpoint attivi. Secondo le stime di Statista, il numero di dispositivi Internet of Things (IoT) in tutto il mondo arriverà ad oltre 29 miliardi di dispositivi IoT nel 2030.
Nelle Smart Factory, l’approccio Lean applicato al digitale consentirà di migliorare i processi manifatturieri grazie all’integrazione tra IT (Information Technology) e OT (Operation Technology) e all’enorme quantità di dati disponibile in real time che, analizzata attraverso Intelligenza Artificiale e Machine Learning, renderà possibile un approccio data-driven sulla base del quale guidare il processo decisionale e ottenere insight utili per efficientare la produzione.
5 Tecnologie emergenti che renderanno più efficiente la produzione
Il processo aziendale finalizzato alla realizzazione di un prodotto è caratterizzato da una serie di fasi e attività che vanno dalla ricezione dell’ordine, al prelievo e movimentazione dei componenti, all’assemblaggio, fino alla validazione e collaudo del prodotto finito. In un’ottica lean, le principali tecnologie emergenti che, integrate nel processo della fabbrica, consentono la gestione della pianificazione, dei magazzini e delle postazioni di lavoro, supportandone l’ottimizzazione e il miglioramento, sono: Digital Twin e Virtual Commissioning, Automazione robotica, Logistica 4.0, Produzione snella (Lean 4.0), Digital Backbone.
Digital Twin e Virtual Commissioning: grazie al gemello digitale, un modello virtuale dell’asset che ne replica le funzionalità e la fisicità, simulandone l’interazione con il contesto di riferimento, è possibile analizzare le caratteristiche del processo produttivo e del prodotto, prevenire errori di progettazione e prevedere le performance finali (Digital Twin di processo). Il suo utilizzo a livello di sistema operations supporta analisi costi e performance, pianificazione e controllo, valutazione dei colli di bottiglia, valutazioni di investimenti. Il Virtual Commissioning, ovvero l’utilizzo del Digital twin a livello di macchina, consente infatti di riprodurre il comportamento di un sistema reale in un ambiente virtuale, per testarlo e ottimizzarlo prima della sua produzione. Integrando automazione e meccanica, il Digital Twin della macchina permette una qualità in fase avviamento più elevata.
Automazione robotica: l’implementazione di processi robotici automatizzati consente la gestione e il controllo del processo, standardizzando le attività lavorative e incrementando la produzione, con costi inferiori e maggiore precisione e affidabilità. In ottica Lean 4.0, inoltre, favorisce la creazione di una postazione di lavoro più performante in termini di efficienza e di qualità, apportando notevoli benefici nell’operatività di una postazione di assemblaggio tipica del contesto manifatturiero italiano. La condivisione di ambienti lavorativi tra operatori e robot collaborativi (cobot) permette di assistere il lavoratore nei diversi processi dell’industria manufatturiera, portando benefici cognitivi, ergonomici e fisici.
Logistica 4.0: con questo termine si fa riferimento ad un cluster di tecnologie a supporto della movimentazione e della tracciabilità delle merci nella filiera produttiva, quali sensoristica IoT e RFID (Radio Frequency IDentification), sistemi di picking pick-to-light, robot AGV (Automated Guided Vehicles) e sistemi di localizzazione RTLS (Real Time Locating System), software di middleware e orchestrator. Queste tecnologie e sistemi permettono un controllo istantaneo della qualità di processo, riducendo al minimo sprechi derivanti dall’accumulo inutile di risorse, e il monitoraggio continuo di ogni componente del prodotto con il quale si costruisce e si alimenta il modello digitale di processo che, a sua volta, consente di avere una visione olistica dell’intera produzione, ottimizzando i processi, l’avanzamento della produzione e favorendo il coordinamento delle risorse in termini di spazio e tempo.
Produzione snella 4.0: grazie a questa metodologia nell’approccio alle operations, è possibile avere sistemi di produzione più efficienti e flessibili. Le aziende che adottano una metodologia Lean 4.0 sono in grado di sviluppare cicli di produzione lineari, rapidi e sincronizzati all’interno del proprio sistema guidati da logiche Just-in-Time e caratterizzati da una tensione al miglioramento continuo. Tramite il metodo Lean i flussi produttivi vengono riconfigurati in una ottica cliente, riducendo e abbassando tempi di risposta e costi di produzione, e creando, nello stesso tempo, un ambiente più sicuro e partecipativo per i propri dipendenti. Questo approccio, evita all’azienda la digitalizzazione degli sprechi, investimenti inutili o addirittura dannosi per il proprio business, permettendo di perseguire una trasformazione digitale di successo.
Digital Backbone: rappresentata l’infrastruttura software necessaria alla condivisione dei dati e delle informazioni. Capace di interagire con i diversi livelli gestionali dell’architettura del sistema, questa “dorsale digitale” consente di trarre il massimo vantaggio dall’interoperabilità di tutti i fattori produttivi e dallo sfruttamento in tempo reale dei dati; è suddivisa in uno strato software in locale (SW OT), che agisce a livello OT permettendo la comunicazione e l’interfacciamento tra le macchine, e uno in remoto (SW IT) che consente l’orchestrazione dell’ordine e delle BOM (distinta base) e la gestione del magazzino e delle scorte.
In conclusione, grazie a queste tecnologie emergenti la produzione industriale sta subendo profonde trasformazioni, rendendo possibile l'automazione di compiti complessi, riducendo gli errori e aumentando l'efficienza. Nel complesso, le aziende sono in grado di adattarsi più rapidamente ai mutamenti del mercato e rimanere più competitive, nell’affrontare le sfide della duplice transizione Green e Digital.