Smart Factory e gestione produzione ottimizzata: come fare la differenza
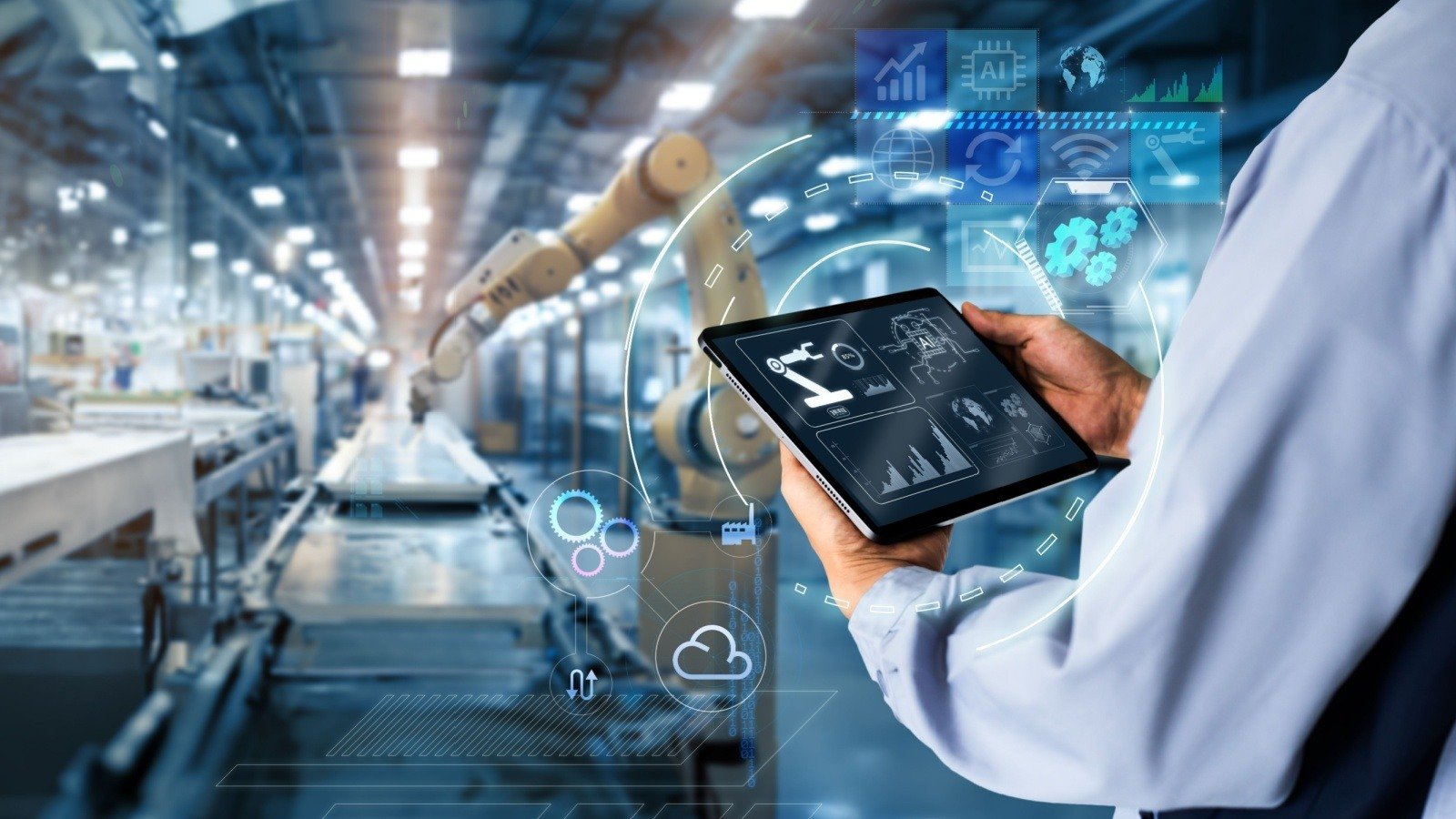
Partiamo da un presupposto: oggi, realizzare una Smart Factory basata sul modello concettuale di un decennio fa non è la strategia migliore. Soprattutto, per quanto concerne l’obiettivo: se da un lato resta fondamentale per qualsiasi struttura operare in chiave di efficienza, di produttività e di abbattimento degli sprechi, oggi occorre ragionare anche in ottica di sostenibilità delle operations (fabbrica sostenibile), di resilienza della struttura e del contesto in cui opera, nonché di integrazione sinergica tra le nuove tecnologie e l’operato (centrale) dell’uomo.
È peraltro chiaro che il paradigma 5.0 non stravolge il concetto di smart factory, ma impone un focus più ampio e sistemico che le aziende possono implementare solo partendo da 4.0, ovvero da una digitalizzazione pervasiva e da una trasformazione data-driven di tutti i loro processi.
Smart Factory: cosa fa la differenza, oggi?
Oggi, le aziende hanno a loro disposizione tutti gli strumenti per vincere le sfide poste da mercati sempre più imprevedibili, complessi e globali. La chiave è sì l’integrazione di tecnologie avanzate, ovvero un percorso corretto di trasformazione digitale, ma lo è anche il mindset giusto – che, come visto, non è quello di un decennio fa – unito alle competenze necessarie per governare scenari complessi e a un approccio fortemente innovativo, con contestuale capacità di trasformare un’idea brillante in una soluzione concreta, in modo veloce ed efficace.
Capacità di ottimizzare la produzione
Ottimizzare la produzione resta il faro che guida l’operato delle imprese. Ha un impatto deciso sulla produttività, sull’efficienza e sulla flessibilità, ovvero sulla capacità di assecondare mercati che richiedono un altissimo livello di personalizzazione e non scendono a patti con la qualità. In sintesi, è ciò che rende l’azienda competitiva.
Nell’ottica della smart factory, lo sguardo va immediatamente alla tecnologia avanzata. Digital twin e intelligenza artificiale, solo per citare qualche manifestazione particolarmente trendy, giocano un ruolo centrale permettendo simulazioni e previsioni precise che migliorano i processi decisionali e molteplici altre attività all’interno dei cicli produttivi (manutenzione degli asset, in primis). Ma va anche sottolineato come l'ottimizzazione non si fermi qui: è essenziale ottimizzare i processi e concentrarsi sempre di più sulla resilienza delle supply chain per rispondere alle sfide globali che tutti conosciamo.
Indirizzare la trasformazione in chiave di sostenibilità
La smart factory di oggi non può limitarsi a ottimizzare la produzione e ridurre i costi. Il time to market è essenziale ma non è l’unica cosa. L’azienda deve anche orientarsi verso la sostenibilità per ridurre il proprio impatto ambientale e creare valore a lungo termine per essa stessa, per la società e il pianeta.
Oggi, la differenza la fanno quelle aziende che valutano le loro operations anche in chiave di sostenibilità, identificano aree su cui è possibile intervenire e agiscono di conseguenza, spesso proprio attraverso la trasformazione digitale. Tecnologie come l'Internet of Things (IoT) o sistemi di automazione che migliorano l'efficienza dei processi produttivi possono avere un impatto chiave in ottica di sostenibilità, che ovviamente si somma all’impiego di energie rinnovabili, all’abbattimento degli sprechi e alla revisione dei processi nell’ottica della circolarità.
Sostenibilità è anche centralità dell’essere umano in un paradigma industriale che sembrava virare quasi completamente verso l’automazione. Una smart factory “che fa la differenza” garantisce un ambiente di lavoro sicuro e inclusivo, e soprattutto stimola la collaborazione uomo-macchina, uno degli elementi fondanti di questa trasformazione.
Le competenze giuste
I processi produttivi moderni sono sempre più complessi e richiedono competenze avanzate per essere gestiti efficacemente. Gli operatori sul campo e le figure dedicate alla supervisione devono possedere una combinazione di conoscenze tecniche e capacità se vogliono sfruttare appieno le tecnologie dell'Industria 4.0 e prepararsi alle sfide dell'Industria 5.0. Solo così è possibile perseguire la vera ottimizzazione dei processi produttivi, e quindi competitività in tempi complessi come questi.
Saper stimolare e gestire l'innovazione
L'innovazione è la chiave per risolvere problemi produttivi come i downtime, la gestione delle scorte, l’ottimizzazione degli attrezzaggi e dei lead time. In contesti molto sfidanti, le aziende dovrebbero creare un ambiente in grado di stimolare creatività e innovazione, incoraggiando la sperimentazione e l'adozione di nuove tecnologie. Ciò significa anche integrare nativamente i principi del paradigma 5.0, come la sostenibilità e la centralità dell'essere umano, nei processi di innovazione. Molto importante, a tal fine, è farsi assistere da partner competenti, che evitino alle aziende di sprecare tempo e budget.
Capacità di gestione del cambiamento
La capacità di integrare le nuove tecnologie nel contesto esistente e di gestire il cambiamento è fondamentale. La gestione del cambiamento, in particolare, è un processo continuo, che richiede comunicazione efficace, coinvolgimento di tutti e adattabilità. Le aziende che riescono a integrare continuamente nuove tecnologie evitando gli effetti nocivi della discontinuità sono quelle che riusciranno a prosperare nell'era 5.0. E di sicuro anche in quelle seguenti.