Il progetto ROPPENP di Limea-Fisma: metodologia LEAN Manufacturing per il miglioramento continuo dei processi produttivi
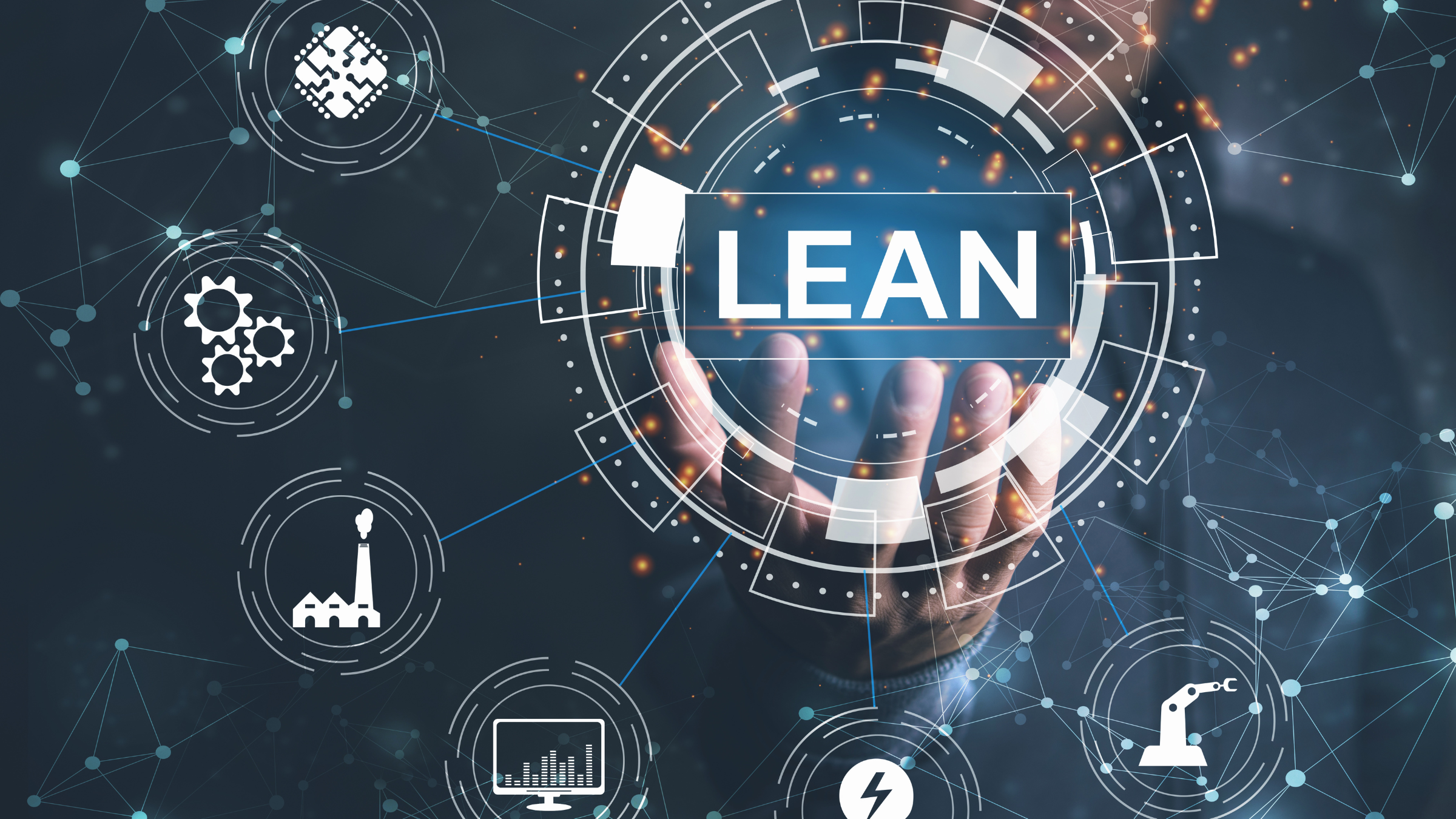
Il progetto ROPPENP, acronimo che sta per “Ridefinizione Organizzativa del Processo Produttivo nel plant attuale E definizione delle attività produttive per il Nuovo Plant”, nasce dalla volontà di Limea-Fisma Spa, importante realtà industriale internazionale con sede a Marcallo con Casone (Mi), leader nella produzione di imballaggi metallici in banda stagnata per uso industriale, di voler intraprendere una revisione delle proprie linee produttive in ottica Lean Manufacturing al fine di conseguire un significativo aumento della produttività attraverso la riorganizzazione dei propri flussi produttivi.
Gli attuali processi produttivi di Limea-Fisma, infatti, prevedono l'uso di macchinari e linee automatizzate asservite per mezzo di attività manuali, dispersive per loro natura. Ne risulta un flusso dei materiali poco lineare, da cui consegue una scarsa efficienza produttiva che una profonda rivisitazione dei processi permetterebbe di incrementare, consentendo un efficientamento della produzione. La ridefinizione organizzativa dei processi prevede anche la valutazione dell’eventuale introduzione di magazzini automatici e le sinergie derivanti dalla costruzione di un secondo plan produttivo, limitrofo al primo già esistente.
Grazie all’attività di consulenza tecnologica fornita da MADE4.0, a cui l’azienda si è rivolta per avere un supporto negli studi di fattibilità finalizzati al miglioramento continuo dei processi produttivi con un approccio Kaizen, Limea-Fisma è riuscita a conseguire importanti miglioramenti nella capacità produttiva in termini di competitività, sicurezza e sostenibilità.
Dall’attività di studio condotta dai consulenti di MADE4.0 e dal confronto degli ipotetici scenari di layout per l'allocazione delle linee produttive (nuove ed esistenti) che permetterebbero di incrementare ed efficientare la produttività dell’azienda, una volta identificata la migliore soluzione, il progetto ha consentito di sviluppare unasimulazione 2D del layout in grado di restituire l'analisi dei colli di bottiglia e, in generale, di aumentare la capacità produttiva garantendo l'ottimale flusso del processo, dall'ingresso delle materie prime fino all'uscita del prodotto finito dal magazzino dello stabilimento, come strumento a supporto del processo di decision making.
Il progetto ROPPENP
Nel dettaglio, l’intento dell’azienda, impegnata non solo nella produzione di contenitori metallici di qualità certificata ad uso professionale ma anche nella fornitura di un’ampia gamma di imballaggi omologati per il trasporto di merci pericolose, era quello di realizzare, grazie al supporto di MADE4.0, un «Programma Kaizen per l'Eccellenza» con l’obiettivo di:
- ottimizzare i flussi produttivi e di processo presenti nell’attuale plant al fine di aumentare la produttività attraverso uno studio che prevedesse anche la valutazione dell’introduzione nel plant di un magazzino automatico per semilavorati e/o prodotti finiti, attualmente assente;
- definire le attività e i processi per un secondo plant produttivo, di prossima realizzazione.
Il progetto di ridefinizione organizzativa del processo produttivo, basata sulla simulazione dei processi nuovi ed esistenti, prevede un approccio decisamente innovativo per un produttore di medie dimensioni di imballaggi metallici per uso industriale, che può portare miglioramenti innovativi e concreti di cui solitamente possono beneficiare solo i big player che operano dei settori dell'imballaggio per food e beverage.
L'installazione di uno o più magazzini automatici e la creazione di spazio disponibile per ulteriore automazione, sia nel nuovo plant sia in quello attuale, consentiranno non solo un efficientamento della produzione e l'avvio di nuovi progetti in ottica 4.0, ma anche una riduzione dei consumi energetici, che beneficeranno della riduzione dei trasporti interni.
Inserendosi nel solco della cosiddetta Lean Automation, l'innovativo approccio progettuale, grazie a soluzioni di automazione avanzata, sistemi di controllo intelligente e alla digitalizzazione, consente di definire un sistema di produzione altamente efficiente, flessibile e di alta qualità che può adattarsi meglio alle esigenze mutevoli del mercato, migliorando la competitività dell’azienda.
Con l'adozione dell'approccio metodologico Kaizen a livello di cultura organizzativa, inoltre, Limea-Fisma ha inteso favorire la creazione di un ambiente innovativo in cui il miglioramento continuo è abbracciato da tutti i membri dell'organizzazione, coinvolgendo tutti i dipendenti a tutti i livelli nell'identificazione dei problemi e nella ricerca di soluzioni. A questo scopo, il progetto ha previsto anche il coinvolgimento dei collaboratori di Limea-Fisma, che sono stati ingaggiati e incoraggiati dai consulenti MADE4.0 nel proporre miglioramenti e a partecipare attivamente al processo di implementazione.
I dettagli del progetto
Per aumentare la produttività globale della fabbrica utilizzando al meglio i futuri investimenti, il progetto è stato articolato in 3 fasi (Work Packages):
- l’analisi dei flussi produttivi “end to end” per condividere le opportunità di miglioramento (Value Stream Globale «end to end»);
- la generazione del nuovo modello produttivo e del layout generale (vecchio e nuovo plant) e la valutazione delle alternative di organizzazione;
- la valutazione delle alternative di investimento e relative payback.
Nell'ambito della fase WP1, i consulenti di MADE4.0 hanno esaminato i volumi produttivi 2023 e le proiezioni per il 2024, suddividendoli tra le linee di prodotto attualmente presenti e valutandone l’impatto sulle singole linee; utilizzando lo strumento dell'Overall Equipment Efficiency (OEE) collegato al mix produttivo, è stata analizzata la performance degli attuali impianti tecnologici, in termini di efficienza, qualità ed affidabilità. Nell'ambito di questa attività, è stata effettuata una segmentazione per cliente/prodotto/processo e sono stati individuati i nuovi concept da introdurre a valle del Value Stream globale.
Nell'ambito del WP2, i consulenti di MADE4.0 hanno analizzato il flusso fisico dei materiali “end to end”, lungo tutta la linea produttiva, dal magazzino materie prime al prodotto finito, valutando i MUDA (sprechi) di processo e i costi legati all'attuale modello produttivo. Relativamente alla supply chain, sono stati valutati anche il profilo di stock ed il livello di servizio, identificando le eventuali criticità presenti.
Infine, sono stati definiti i macro obiettivi di progetto (qualità, efficienza e livello di servizio) da raggiungere con la riorganizzazione del modello produttivo, contemplando anche la possibilità di fruire di nuovi spazi e tecnologie disponibili in futuro. Quindi, è stato sviluppato il nuovo modello produttivo, partendo dalla definizione delle regole per un concept layout e arrivando al block layout generale nel quale sono stati posizionati i macro flussi produttivi negli stabilimenti, rendendo visibili lo spazio occupato, la macro organizzazione e il dimensionamento di massima degli spazi.
A questo punto delle attività, nella fase WP3, MADE4.0 si è occupato della valutazione delle alternative tecnologiche più in linea con gli obiettivi definiti nella fase iniziale ed è stato predisposto il layout fisico, condividendo con la direzione dell’azienda il piano esecutivo per messa in opera del nuovo modello, progettato per aumentare la produttività aziendale.
Impatto atteso e ricaduta sulla capacità produttiva
Grazie all’attività di consulenza tecnologica fornita da MADE4.0 e al ruolo svolto dai suoi consulenti all'interno dell'attività progettuale, Limea-Fisma ha potuto beneficiare in tutti i Work Package e i task del progetto di tutto il supporto necessario all’implementazione di soluzioni tecnologiche, organizzative e gestionali atte a migliorare i processi delle imprese in ottica Industria 4.0.
Con la progettualità proposta, Limea-Fisma prevede diverse ricadute e impatti industriali rilevanti, in particolare per quanto concerne i temi di competitività, sicurezza e sostenibilità.
L'ottimizzazione e la re-ingegnerizzazione dei processi in ottica Lean, portando alla riduzione dei trasporti interni e dei tempi di attraversamento, determinano un minore consumo di energia, con impatti importanti sull'OEE e sui consumi energetici. Questo comporterà anche una riduzione di rischi di obsolescenza e danneggiamento dovuti al trasporto, nonché la creazione di spazio per ulteriore automazione dei processi aziendali, congiuntamente ad un miglioramento della tracciabilità e selettività della merce.
Grazie alle iniziative di miglioramento emerse dallo studio progettuale, è stato possibile attuare un percorso di rinnovo delle strutture del magazzino, con conseguente ottimizzazione e riduzione degli ingombri dovuti a stoccaggio di materiale a bordo linea e nelle aree di passaggio, con benefici sia operativi che in termini di rischio correlato alla salute e sicurezza degli operatori.
In termini di risultati attesi, si prevede un aumento della produzione del 10% nel plant attuale, grazie alla reingegnerizzazione dei processi in ottica di miglioramento continuo (continuous improvement), e un ulteriore aumento della capacità produttiva e della standardizzazione dei processi con il nuovo plant, che avrà processi ed attività sinergiche con quello attuale.