Il progetto RAM-ICoS, nuove funzionalità data-driven per l’ottimizzazione del processo e il controllo di qualità nella produzione industriale additiva di componenti di grandi dimensioni (LFAM)
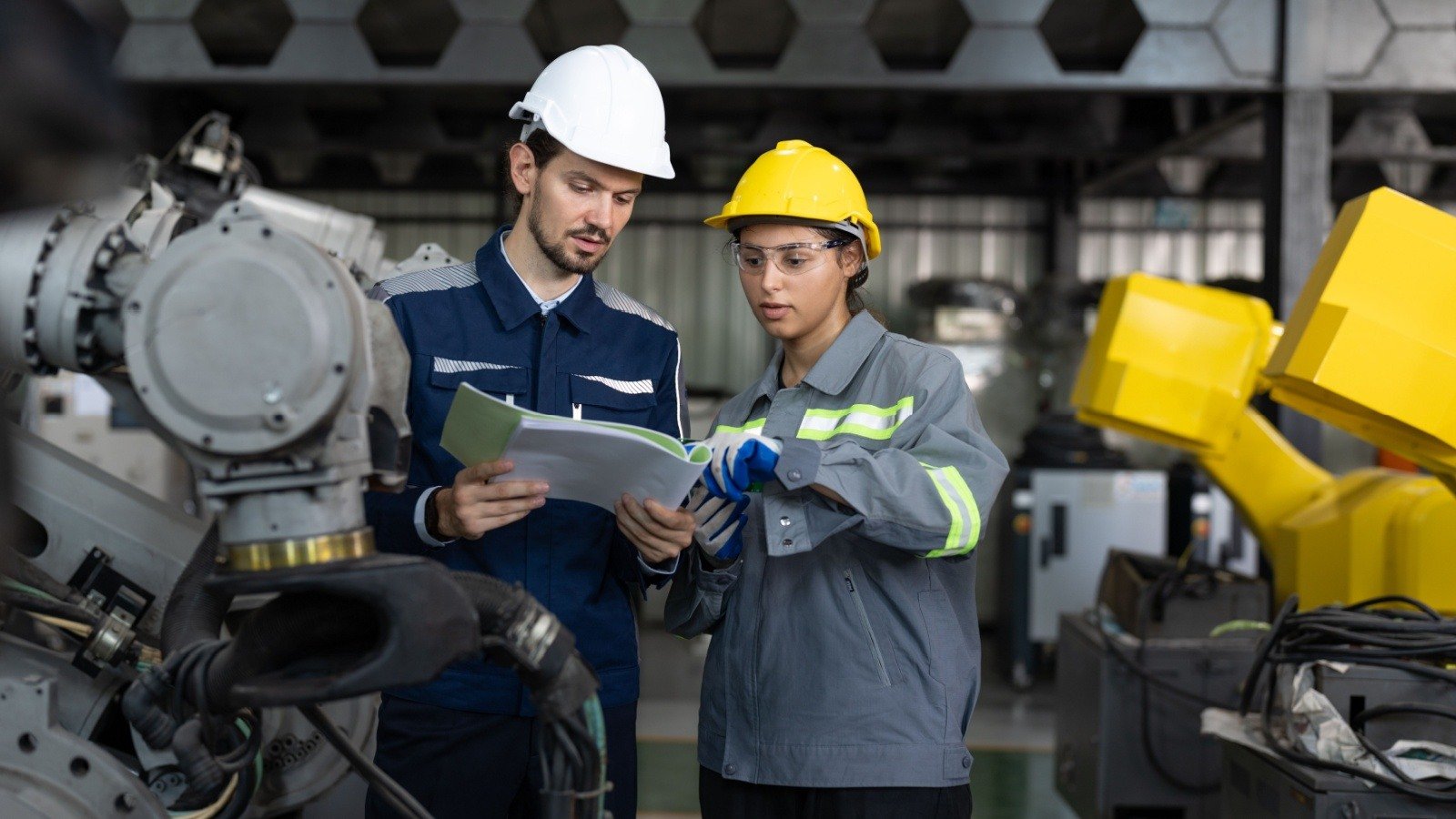
La produzione additiva è una famiglia di tecnologie giovane e in forte crescita, nell’ambito della quale la produzione industriale di componenti polimerici di grandi dimensioni (Large Format Additive Manufacturing, LFAM), in particolare, rappresenta un mercato di nicchia, in cui opera un numero molto limitato di aziende, nonostante la richiesta in continuo aumento di applicazioni di questo tipo. Sul territorio nazionale, Caracol rappresenta l’unica realtà industriale consolidata specializzata nella manifattura additiva avanzata, riconosciuta dal mercato per aver sviluppato una soluzione che integra i supporti robotici con una tecnologia di Additive Manufacturing (Heron AM).
Grazie allo sviluppo hardware di un sistema innovativo di estrusione brevettato e ad algoritmi software proprietari, il sistema robotico di Caracol permette di produrre componenti in monoscocca di dimensioni elevate, con geometrie molto complesse mediante “direct printing” di materiali compositi ad alte performance meccaniche e termiche. L’innovazione di Caracol risiede quindi nel superare i limiti dimensionali delle tradizionali stampanti 3D industriali, con costi operativi inferiori rispetto a processi tradizionali e ad altre soluzioni sul mercato. Caracol è la prima azienda italiana che utilizza sistemi LFAM per produzioni industriali, ad aver ottenuto la certificazione AS/EN 9100 per la gestione di processi in qualità secondo i requisiti dell’industria aerospaziale, caratteristica che necessita di un sistema di miglioramento continuo per mantenere qualità, innovazione, e competitività a livelli adeguati alla fornitura di componenti per il settore.
In un contesto fortemente innovativo e orientato al miglioramento continuo delle soluzioni, quindi, l’esigenza di Caracol era sviluppare un progetto di innovazione per continuare a rendere il processo più robusto e ripetibile, e mantenere su produzioni di scala industriale controllo di qualità richiesto da applicazioni strategiche e di fascia elevata (aerospazio, energia).
L’obiettivo del progetto RAM-ICoS (Intelligent Control System for Robotic Large Scale Additive Manufacturing System), realizzato con il supporto del Dipartimento di Meccanica (DMEC) del Politecnico di Milano e del laboratorio AddMe.Lab dedicato allo studio, sviluppo e ottimizzazione di sistemi e processi di manifattura additiva, consiste nel dotare il sistema di controllo robotico esistente con nuove funzionalità di acquisizione ed elaborazione dati in-process da sensori integrati per migliorare la qualità della deposizione e reagire, in tempo reale, ad eventuali anomalie in ottica zero-defect manufacturing.
Per questo progetto di innovazione, Caracol si è avvalsa dei servizi e delle competenze di MADE4.0 per integrare il proprio know-how in merito alla conoscenza delle tecnologie di sensorizzazione, monitoraggio e controllo data-driven del processo, per abilitare l’automazione industriale richiesta per l’implementazione di queste tecnologie.
Il progetto RAM-ICoS
Anche a livello internazionale, il controllo di processo è un aspetto ancora critico e oggetto di ricerca. Infatti, nonostante la necessità di un controllo di processo preciso e di un monitoraggio in grado di tracciare i parametri di processo lungo tutto il processo produttivo rappresenti un punto di importanza primaria, soprattutto in settori che richiedono alte prestazioni e stringenti requisiti di qualità, come quello aerospaziale, i pochi sistemi presenti in letteratura, di fatto, rappresentano prove di concetto o soluzioni prototipali che necessitano di importanti sviluppi per raggiungere una completa industrializzazione.
Come già anticipato, l’obiettivo dell’attività di progetto consiste nel dotare i sistemi robotici LFAM di Caracol di nuove capacità data-driven per l’ottimizzazione del processo. Il progetto prevede lo studio e la verifica sperimentale di nuove soluzioni di sensorizzazione per l’acquisizione in-linea di dati multi-sorgente per tenere sotto controllo lo stato di funzionamento del sistema (i.e., estrusore) e caratteristiche di qualità legate alla deposizione. I risultati di questo progetto permetteranno, in una successiva fase di sviluppo industriale, di mettere a punto soluzioni innovative di controllo dei sistemi robotici in grado di adattare le strategie di deposizione in base alle misurazioni effettuate in linea, per ridurre l’insorgenza di difetti e massimizzare qualità e prestazioni dei prodotti realizzati.
La milestone principale del progetto è la realizzazione di un dimostratore (PoC) in grado di dimostrare le nuove funzionalità sviluppate e supportare i successivi passi di industrializzazione, per la cui realizzazione MADE ha fornito a Caracol supporto per le attività di implementazione dell’hardware (robot, computer e sensoristica) e del software necessari.
Nel dettaglio, le principali attività di MADE sono consistite nel:
- supportare Caracol nell’individuazione delle problematiche del processo oggetto dell’analisi (Robotic LFAM System), nella definizione e caratterizzazione dei relativi difetti che possono essere generati durante la deposizione attraverso uno studio ad-hoc, condotto anche tramite modellazione fisico-matematica del processo;
- identificare le tipologie di sensori e la loro corretta collocazione all’interno del sistema di stampa per raccogliere le informazioni idonee per il monitoraggio e controllo del processo;
- progettare una campagna sperimentale per valutare l’efficacia delle soluzioni di sensorizzazione proposte (termocoppie e sensori di pressione per misurazioni relative allo stato degli estrusori e pirometri e/o altri sensori ottici per le misure sulle caratteristiche del layer);
- progettare una campagna sperimentale per studiare le problematiche di qualità relative a diversi materiali di interesse con particolare riguardo ai polimeri fibro-rinforzati e a nuovi materiali non ancora utilizzati da Caracol;
- identificare un sistema di raccolta e analisi dei dati in grado di identificare le anomalie e supportare il processo di presa delle decisioni.
Le fasi del progetto RAM-ICoS
Il progetto ha previsto l’analisi delle criticità dell’attuale sistema produttivo di Caracol, dei difetti associati ai diversi materiali e strategie di deposizione, e dei differenti materiali utilizzabili. Oltra a ciò, è stata messa a punto una nuova sensorizzazione del sistema di stampa accoppiata ad un sistema di acquisizione, trattamento e analisi dei dati, il tutto integrato in un dimostratore funzionante in ambiente operativo.
Nel dettaglio, le attività di progetto sono state implementate attraverso i seguenti 4 pacchetti di lavoro:
- WP1 – Analisi della difettosità di processo. La prima fase ha previsto lo studio del processo di stampa e della soluzione robotica per l’identificazione e la definizione dei difetti e delle anomalie di interesse (tipologie di difetto, root cause, modalità/meccanismi di formazione, livelli di severità, impatto su qualità e prestazioni finali, etc.);
- WP2 – Sensorizzazione del sistema robotico. L’attività è stata condotta in parallelo con il WP1 e il WP4 per acquisire la migliore conoscenza possibile dalle diverse fonti di segnali, comprendendo anche la conoscenza progettuale di Caracol. Il coinvolgimento di Caracol ha riguardato la conoscenza progettuale della soluzione di AM robotics oggetto del progetto e quindi la definizione dei requisiti di compatibilità per l’integrazione dei sensori nella soluzione.
- WP3 – Raccolta e analisi dei dati. Tale attività ha avuto l’obiettivo di valutare l’efficacia delle soluzioni di sensorizzazione identificate nel WP2, i loro pro e contro, nonché i limiti e le possibilità di miglioramento/tuning della qualità dei segnali acquisiti. In questa fase è stata condotta una campagna sperimentale durante la quale sono stati realizzati componenti stampati con materiali differenti e identificate le condizioni di stampa (strategie di deposizione, feature geometriche critiche, parametri di processo) sulle quali è possibile agire per indurre l’insorgenza di difetti e anomalie di processo, al fine di identificare sperimentalmente la capacità di identificazione automatizzata (detectability, prestazioni in termini di falsi allarmi e mancati allarmi, sensibilità del segnale a disturbi e variazione delle condizioni operative, etc.).
- WP4 – Realizzazione del dimostratore. Questa fase conclusiva ha visto la realizzazione di un sistema prototipale (PoC) costituito dall’integrazione di sensori nel sistema di stampa, da una piattaforma per la raccolta dati e dal metodo per l’analisi dati in-linea sviluppato nel WP3, in grado di identificare automaticamente le anomalie di stato macchina e processo. La realizzazione del dimostratore ha coperto tutta la durata del progetto poiché è partita dalla progettazione di un sistema robotico di stampa pensato e dedicato alle attività sperimentali del progetto, è continuata con la sua realizzazione e si è conclusa con il PoC che ingloba le funzionalità innovative sviluppate. Il processo di estrusione, che è oggetto principale dell’innovazione di questo progetto, viene controllato da un sistema hw/sw progettato ad hoc da Caracol. In tal modo, si è potuta garantire l’adeguata flessibilità della soluzione per accogliere i nuovi sensori ed integrare l’intelligenza a bordo.
Nello sviluppo di queste attività, MADE4.0 ha fornito un servizio di:
- consulenza tecnologica e supporto all’implementazione delle tecnologie digitali e loro ottimizzazione mediante studi di fattibilità finalizzati all’implementazione di soluzioni tecnologiche, organizzative e gestionali atte a migliorare i processi in ottica Industria 4.0;
- scouting tecnologico per l’individuazione delle tecnologie e dei partner tecnologici più adatti a sviluppare l’innovazione di prodotto e di processo, definendo una strategia tecnologica aziendale coerente con i trend che caratterizzano il settore.
Impatto atteso e ricadute nel settore industriale di riferimento
Il progetto comporta un’evoluzione delle parti che potranno essere prodotte con la tecnologia Heron AM di Caracol dal punto di vista del controllo di processo e, quindi, del controllo qualità. Avere la possibilità di monitorare e correggere il processo di stampa 3D, grazie alla sensoristica sia attiva che passiva, consente non solo di diminuire sensibilmente il lead-time tra le fasi prototipali e la messa in produzione in serie di parti funzionali, ma anche di intraprendere attività di manufacturing per settori ad altissima performance.
Sarà, infatti, possibile stampare componenti con maggiore precisione, riducendo di molto gli errori e le non conformità derivanti dal processo di stampa. Questo permetterà di ridurre la numerosità delle parti che, oggi, vengono scartate a causa degli errori di processo e derivanti da difetti tecnologici.
Ne consegue, quindi, l’aumento del numero di parti prodotte “first-time on-quality” e la riduzione dei costi, stimata almeno del 30%, che l’azienda sostiene attualmente per la non-qualità.
Questo consentirà la possibilità di offrire sul mercato soluzioni e prodotti ancora più competitivi, grazie alla maggiore efficienza guadagnata. Da questo vantaggio competitivo, grazie ad una riduzione degli scarti ed un’ottimizzazione dei flussi di produzione, deriverà una ricaduta immediata, sia in termini tecnici che economici, anche su altri settori industriali all’interno dei quali l’azienda opera, quali ad esempio la nautica, l’energy, i settori del design e architettura.
Grazie al nuovo sistema di controllo implementato, nei settori altamente regolamentati, quali l’aerospaziale e l’automotive, all’interno dei quali l’azienda punta a crescere nei prossimi anni, sarà inoltre possibile aggredire anche applicazioni critiche, ad esempio strutture primarie e secondarie, consentendo a Caracol di completare il proprio range di offerte e servizi.
Per quanto riguarda l’attrattività e la competitività, l’aumento della produttività dei sistemi di large format additive manufacturing robotico e della loro efficienza in termini di costi e tempi, favorisce i processi di rilocalizzazione (reshoring, back shoring) delle imprese all’interno del territorio nazionale.
Infine, il controllo e monitoraggio dei parametri di processo e delle condizioni operative permette di identificare varie tipologie di guasti e malfunzionamenti, compresi quelli che possono causare situazioni di rischio sia per l’equipaggiamento che per gli operatori. Anche la riduzione delle attività di supervisione in situ della produzione, grazie alla possibilità di gestione dei sistemi con strumenti informatici da remoto, consente la riduzione del livello dei rischi degli operatori.