Industry 4.0: soluzioni integrate, dalla progettazione al Field Service
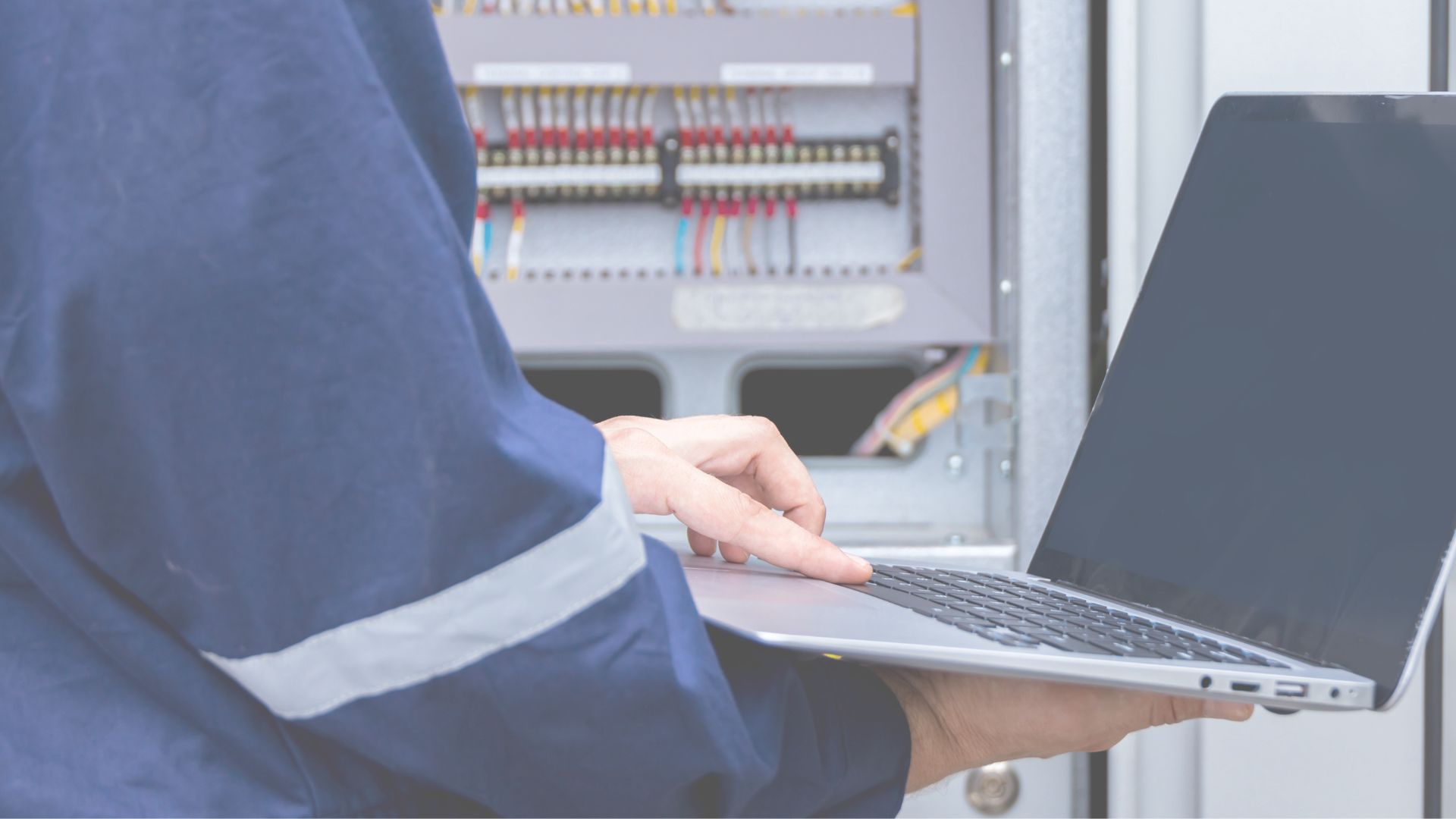
La Demo Experience organizzata da MADE Competence Center con i partner Siemens e SAP e con la partecipazione di TeamViewer e Engineering, ha sottolineato l’importanza dell’integrazione tecnologica e della continuità del dato lungo il ciclo di vita del prodotto. L’obiettivo era dimostrare come una corretta gestione del dato possa migliorare l’efficienza e l’efficacia dei processi, anche grazie alla corretta integrazione di player e soluzioni differenti.
Parafrasando un qualsiasi dizionario, la voce “integrazione” viene descritta come l’atto di completare ciò che risulta insufficiente a un determinato scopo. Nell’accezione informatica, le soluzioni integrate permettono di esaltare ed estendere le funzionalità di singole tecnologie (potenzialmente offerte da soggetti differenti), sprigionando nuove opportunità per il business. In ambito manifatturiero, ad esempio, la combinazione di applicazioni e strumenti digitali permette di ottenere un flusso di informazioni univoco e una visione olistica lungo l’intero ciclo di vita del prodotto, con la possibilità di ottimizzare i processi e abilitare nuove funzionalità.
L’importanza dell’integrazione nell’Industria 4.0 è stato il fil rouge della Demo Experience organizzata da MADE4.0 insieme ai partner Siemens e SAP e con la partecipazione di TeamViewer ed Engineering.
PLM, digital thread e progettazione collaborativa
Per le aziende manifatturiere che vogliono rimanere competitive sul mercato diventa fondamentale adottare soluzioni integrate lungo l’intero ciclo di vita del prodotto abilitando il digital thread, ovvero un flusso di dati univoco e a circuito chiuso che connette mondo reale e virtuale in un rimando continuo.
Radu Simionescu, Senior PLM Consultant di Siemens, ha illustrato come grazie al “filo digitale” si possa abilitare la progettazione collaborativa di prodotti e processi. Il modello avallato è il Closed-Loop Digital Twin che permette lo scambio bidirezionale di informazioni tra asset fisici e gemelli digitali, in un anello chiuso.
Siemens mette al centro del framework la piattaforma PLM Teamcenter, che permette di ottimizzare il digital thread e la collaborazione tra diversi dipartimenti attraverso il ciclo vitale del prodotto. Il software garantisce la gestione strutturata e univoca dei dati, con un sistema di controlli per regolare l’esecuzione degli accessi e delle modifiche.
Teamcenter permette l’integrazione con il gestionale SAP e le soluzioni TeamViewer per l’accesso e il supporto remoto, come dimostrato nel caso di successo Bonfiglioli. Il produttore bolognese, specializzato in riduttori, motori elettrici e inverter, infatti ha adottato il PLM di Siemens per connettere il sistema SAP in uso, standardizzare i processi di sviluppo in tutte le filiali italiane ed estere, configurare le regole per la creazione delle distinte (BOM - Bill Of Materials). A valle del progetto, è stata implementata la piattaforma Frontline di TeamViewer, che sfrutta le tecnologie di Augmented Reality (AR) per assistere gli operatori industriali all’interno degli impianti. Le distinte di produzione generate in Teamcenter vengono arricchite di contenuti AR, quindi trasmesse a TeamViewer e, dopo ulteriori elaborazioni, rese disponibili agli addetti sul campo.
Evoluzione del Service, come cogliere l’opportunità
In continuità con quanto illustrato precedentemente, Piero Basso, Senior Solution Advisor di SAP Italia, ha affrontato il tema del Service e come, grazie alle tecnologie digitali, anche questa fase sia evoluta. La manutenzione infatti sta cambiando sulla spinta del cloud computing, intelligenza artificiale, connettività e dispositivi mobile. Mentre prima veniva eseguita internamente da personale aziendale, oggi può essere concepita come servizio erogato da fornitori terzi, che hanno l’impellenza di ottimizzare le risorse, le tempistiche e la qualità degli interventi.
Per rispondere alle necessità di mercato, SAP propone un sistema integrato di soluzioni per il Service Management, che permette di gestire in continuità la componente di assistenza clienti, Service Operations e interventi sul campo.
All’interno del framework, la piattaforma Field Service Management permette di gestire l’assistenza in loco con il supporto dell’intelligenza artificiale. Ad esempio, può semplificare il processo di planning & dispatching. Ricevuta la segnalazione di guasto, l’addetto alla pianificazione può decidere se programmare l’intervento manualmente, avvalersi dei suggerimenti del sistema oppure sfruttare gli algoritmi AI per la schedulazione automatica. Incrociando i dati a sistema con fonti esterne, l’artificial intelligence assegna il task al tecnico ottimale, selezionato secondo diversi criteri: competenze richieste, disponibilità, distanza geografica, condizioni del traffico in tempo reale e così via.
L’integrazione di SAP Field Service Management con le soluzioni di TeamViewer permette di affinare ulteriormente la pianificazione dell’assistenza, grazie alle informazioni fornite dagli operatori sul campo.
Realtà aumentata e assistenza remota nei processi industriali
A dettagliare le potenzialità delle tecnologie TeamViewer, in particolare della piattaforma Frontline per l’assistenza remota sui processi industriali, è Carlo Bertozzi, Senior Enterprise Account Executive della multinazionale tedesca.
Le soluzioni TeamViewer per esempio possono abilitare un collegamento con un esperto, che può fornire supporto tecnico a distanza visualizzando lo schermo del richiedente oppure, nel caso di Frontline, scambiando informazioni attraverso visori e altri strumenti AR. L’assistente remoto visualizza ciò che vede l’operatore sul campo e può essere in grado di fornire una serie di guide, con flussi di lavoro e immagini 2D o 3D, per svolgere attività ordinarie o emergenziali.
Tra le caratteristiche della piattaforma, Bertozzi cita la recente introduzione di funzionalità AI, l’integrazione nativa con gli ambienti in uso (ad esempio, Siemens Teamcenter e SAP Field Service Management) e l’agnosticismo tecnologico rispetto ai dispositivi.
Continuità del dato: abilitatore di sostenibilità
La centralità della continuità del dato viene evidenziata anche da Fabio Raffo, EMEA Solution Strategy Director, multinazionale italiana che si presenta nel ruolo di ”ecosystem integrator”.
In particolare, Engineering si è concentrata a dimostrare sull’importanza della continuità del dato per realizzare business case sostenibili, che possono essere trasformati in progetti scalabili.
Citando McKinsey, Raffo ha puntato l’attenzione sulla Generazione Z entrata da qualche anno nel mondo del lavoro, sta mostrando delle caratteristiche distintive che le aziende devono tenere in considerazione: tende a perdere rapidamente l'entusiasmo per il lavoro e mostra una bassa propensione a chiedere consigli ai colleghi più esperti, preferendo il self-learning attraverso video e tutorial. Questo il motivo per cui sarà sempre più strategico creare esperienze gratificanti e utilizzare strumenti digitali appropriati.
Per soddisfare queste nuove esigenze emergenti, sarebbe auspicabile implementare iniziative di Extended Reality (XR), che fanno leva su tecnologie di Virtual, Mixed e Augmented Reality, nonché su strumenti per l’assistenza remota.
Engineering propone un approccio strutturato che permette di affrontare con successo i progetti XR, superando le barriere più comuni (scarso engagement della forza lavoro e commitment dei C-Level; mancanza di governance e conoscenza condivisa; poca visione di insieme e lungimiranza).
Partendo dalla definizione della governance come prerequisito, il percorso proposto si articola in quattro fasi: valutazione preliminare e selezione dello use case in ottica strategica, con reperimento delle informazioni abilitanti; definizione dei controlli e degli obiettivi con monitoraggio delle performance in corso d’opera; condivisione globale dell’esperienza all’interno dell’organizzazione; scaling dell’iniziativa sui diversi impianti.
Infine, per non cadere nella trappola del proof-of-concept ma garantire la sostenibilità dei business case, è fondamentale che il dato rimanga consistente, attraverso le diverse fasi del processo, i layer tecnologici che compongono la piattaforma XR e tutti gli impianti aziendali.
Integrazione è la parola d’ordine
Le soluzioni e i progetti presentati durante la Demo Experience hanno messo in luce come l’integrazione di tecnologie e workflow sia il fattore chiave per migliorare l’efficienza e l’efficacia dei processi lungo il ciclo di vita del prodotto, dall’ingenierizzazione alla manutenzione sul campo. L’interoperabilità dei dati tra ambienti diversi e la costruzione di una base univoca sono fondamentali per ottenere una visione olistica sul product lifecycle, prendere decisioni strategiche e generare valore competitivo per l’azienda.
MADE Competence Center Industria 4.0, sfruttando le competenze dei propri partner, può aiutare la tua impresa nell’implementazione di soluzioni tecnologiche integrate per un efficientamento dei processi e una maggiore competitività sul mercato.