Demo Experience - Accelerare la crescita, strategie pratiche per l’implementazione dell’AI nelle PMI
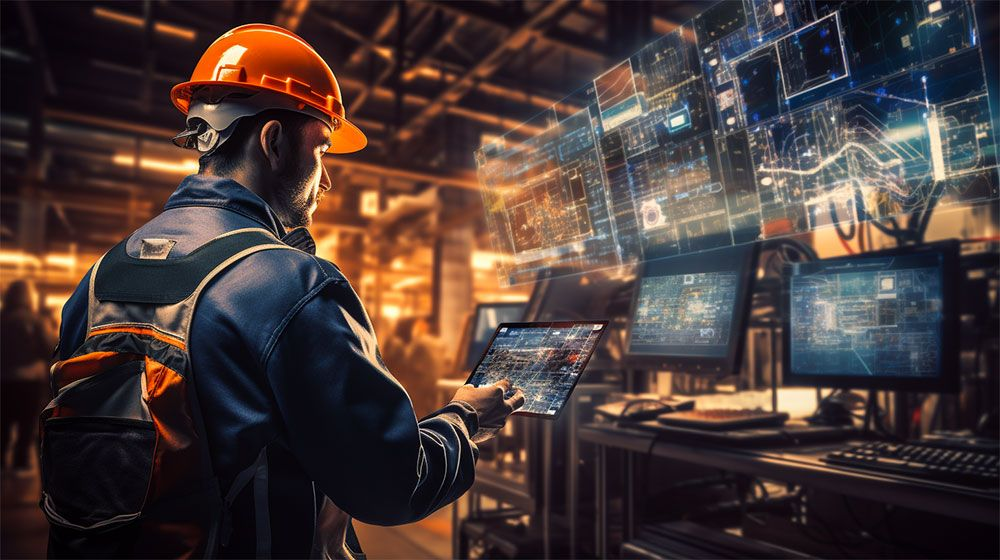
La Demo Experience organizzata da MADE 4.0 in MECSPE, in collaborazione con Tecniche Nuove Media, verteva su Intelligenza artificiale e AI generativa applicata alle PMI dell’industria manifatturiera. I partner di MADE Competence Center, aizoOn, Avvale, Quin e Zerynth, hanno dimostrato come le soluzioni sviluppate grazie ad algoritmi di intelligenza artificiale siano già implementabili oggi, con risultati di efficienza operativa e ottimizzazione delle risorse e dei consumi.
Le applicazioni di intelligenza artificiale danno un vantaggio competitivo alle PMI per efficienza, sostenibilità e ottimizzazione dei processi e delle risorse. Sono due le ‘barriere all’ingresso’ di questa tecnologia in fabbrica. La prima è il livello di cultura digitale dell’azienda: inserire processi basati su AI richiede la presenza di tecnologie capaci di raccogliere e gestire dati consistenti per istruire i modelli. La seconda è la difficoltà di rendere il modello credibile e spiegabile a chi, con il modello, deve interagire.
Durante la demo experience è stato illustrato come il Centro di Competenza MADE, grazie ai propri partner, possa supportare le aziende anche nel processo di adozione di soluzioni basate sull’AI, rispondendo ai timori legati all’utilizzo di questa tecnologia.
Permettere all’intelligenza artificiale di intervenire sui processi aziendali può abilitare un aumento di produttività ed efficienza, del singolo macchinario (es. efficienza energetica, resa e durata) fino all’intero processo produttivo. L’AI ha un impatto sui diversi processi: permette un’ottimizzazione della Supply Chain; rende possibile un maggiore controllo della qualità e abilita concetti come la manutenzione predittiva degli impianti. Inoltre, grazie all’intelligenza artificiale generativa, che utilizza il linguaggio naturale (Large Language Model - LLM), “dialogare” con la macchina diventa sempre più semplice, permettendo un facile accesso ai dati e prendere decisioni strategiche più velocemente.
I vantaggi dell'AI applicata alle macchine industriali
- Riduzione dei costi operativi e aumento dell’efficienza, grazie all’automazione. L’AI viene utilizzata per automatizzare e velocizzare una varietà di processi aziendali, quelli ripetitivi, frequenti e time consuming. In questo modo si liberano risorse umane impiegabili per attività a maggiore valore aggiunto, dove servono esperienza e competenze specifiche di contesto.
- Maggiore efficienza operativa grazie all’elaborazione digitale di grandi quantità di dati che arrivano dalle macchine, attraverso sensori e misurazioni.
I dati vengono processati da algoritmi di machine learning che restituiscono informazioni utili per efficientare la produzione. Attraverso tecnologie come il Digital Twin (ovvero il modello digitale del processo produttivo che interpola i dati raccolti con le previsioni simulate) si possono ottimizzare i processi produttivi. Si riducono scarti, sprechi ed errori; si regolano e manutengono in modo ottimale i macchinari in base a una serie di variabili, allungandone il ciclo di vita e la capacità produttiva. - Ottimizzazione dei processi della Supply Chain, abilitata dai dati dell’intera filiera produttiva e dalle serie storiche, elaborati grazie a tecnologia AI. Si possono fare previsioni molto attendibili della domanda (Forecast), pianificando acquisti e produzione e rendendo flessibile l’automazione a seconda dei lotti da produrre di volta in volta.
- Assistenza virtuale intelligente: da automazione a copilot, con una collaborazione sinergica tra uomo e macchina. L’AI generativa può supportare diverse attività aziendali, dalla gestione documentale (manuali d’uso e documenti amministrativi) a quella produttiva. Vengono applicati modelli funzionali a una “knowledge base”, per esempio, sia testuale sia di immagine o video, che permette al sistema di rispondere alle domande dell’operatore con un linguaggio naturale e flessibile nei contenuti.
Le soluzioni dei partner di MADE
I quattro casi d’uso sull’AI realizzati da aizoOn, Avvale, Quin e Zerynth, partner del Competence Center che supportano lo sviluppo di progetti di innovazione, sono soluzioni pensate per rendere solidi e affidabili i modelli matematici nel contesto industriale. Questo ha esigenze applicative molto stringenti per precisione, affidabilità e responsabilità, corrispondenza con il sistema fisico e forti attese applicative. Gli obiettivi dell’adozione di AI nelle line produttive, infatti, puntano a procedure di Smart System (Industria 4.0) e a “Self Adaptive Automation” (correzioni automatiche nelle Operation, guidate da un sistema AI). Le applicazioni per rispondere al livello di sofisticazione richiesto dall’industria manifatturiera richiedono sempre un altissimo grado di personalizzazione.
Copilot con GenAI - i casi di Avvale e Zerynth
L’intelligenza artificiale generativa, secondo la definizione stessa di ChatGPT 4.0, è un tipo di intelligenza artificiale che apprende dai “pattern” (modelli) di dati e li utilizza per creare nuove soluzioni o previsioni, spesso più affidabili di quelli generati dagli esseri umani.
Nel caso presentato da Avvale, si tratta di una soluzione basata sulle funzionalità di AI generativa per creare un sistema interrogabile con domande in linguaggio naturale e in grado di restituire risposte a partire da una knowledge base documentale. L’obiettivo è una sinergia costante tra uomo e macchina. La revisione, la modifica e la convalida delle risposte restano infatti in capo agli operatori, che hanno competenze di contesto e ottimizzano il sistema stesso con i loro feedback. Inoltre, per evitare risposte fuori contesto o non affidabili, si ingegnerizzano una serie di Prompt (domande) e template (modello) per indirizzare le risposte dentro un perimetro definito.
Zerynth, a sua volta, grazie alla sua Industrial IoT & AI Platform, connette in modo veloce, flessibile e sicuro qualsiasi macchinario industriale per monitorare gli impianti e i processi produttivi. Il caso d’uso presentato è Zero, un copilota progettato per il settore manifatturiero con tecnologie AI+IoT, che si collega direttamente ai dispositivi e ai macchinari in officina. Attraverso l’analisi dettagliata dei dati operativi, Zero fornisce insight per identificare e affrontare le inefficienze. Utilizza il linguaggio naturale che facilita l’accesso alle informazioni da parte di direttori di produzione, responsabili della manutenzione ed energy manager.
AI e Digital Twin per ottimizzare i processi produttivi - caso d’uso aizoOn
La velocità di computo dei sistemi AI, in grado di restituire in pochi secondi le migliori soluzioni per migliaia di combinazioni possibili, sarebbe impensabile per la mente umana.
aizoOn ha dimostrato i vantaggi tangibili dell'introduzione del controllo automatico per macchine CNC, sostituendo il controllo manuale dell’operatore. Il carico dei motori è fortemente correlato allo stato di usura dell’utensile e il mantenimento dei parametri di lavoro all’interno della fascia di tolleranza suggerita dal costruttore è praticamente impossibile da ottenere manualmente. L’applicazione del Reinforcement Learning è una operazione complessa per l’elevato numero di variabili e combinazioni possibili. Tuttavia, grazie al Digital Twin di processo e all’uso di una rete neurale di Deep Learning, è possibile ottenere informazioni in tempo reale di tutti i parametri coinvolti, consentendo di prendere decisioni di controllo ottimali per massimizzare l’efficienza del macchinario.
AI e Digital Twin per ottimizzare i processi produttivi - caso d’uso aizoOn
Quin ha illustrato un case study in cui un’azienda ha richiesto di sviluppare un algoritmo capace di assegnare operatori diversi su linee di assemblaggio con lotti mutevoli, in base a fattori quali seniority, esperienza, specializzazione, carico di lavoro. L’operazione manuale che si è voluta digitalizzare era affidata ai capolinea che non avevano visibilità sulle varabili per compiere una scelta efficiente. La complessità del progetto è che l’azienda non era in possesso di dati storici per addestrare l’algoritmo. È stato quindi sviluppato il Digital Twin della linea di assemblaggio e si è cominciato a raccogliere dati. Grazie a questo primo set di informazioni e ai dati simulati (ottimizzati) si è addestrato il modello, consultabile dagli operatori tramite tablet, in ottica di un continuo scambio di informazioni tra l’ambiente reale e quello simulato per garantire la sicurezza delle raccomandazioni. Nonostante sia ancora in fase di test, il progetto ha già portato benefici significativi, tra cui una distribuzione equa del lavoro, meno conflitti, rischi ridotti e miglioramenti nella salute, qualità e produttività complessiva.