Aperitivo Tecnologico - La progettazione industriale ai tempi dell’Industria 4.0
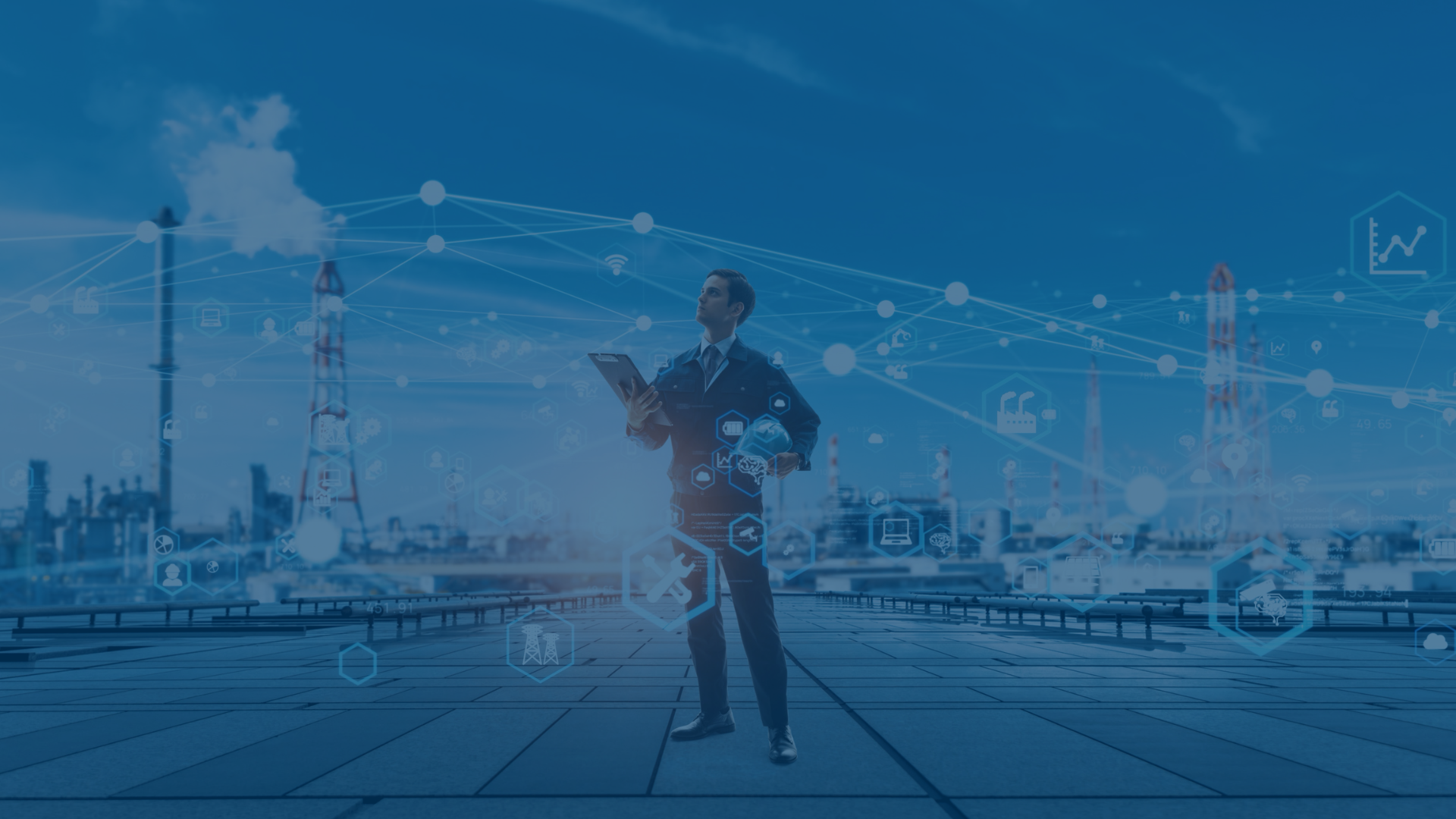
Come cambia la progettazione industriale con le tecnologie digitali? Quali sono i vantaggi per le imprese? MaCh3D, FloFleet, Tecnoinox e Giacomini hanno portato la loro testimonianza al secondo aperitivo tecnologico di MADE Competence Center, in collaborazione con Mecspe e Tecniche nuove.
La progettazione industriale sta subendo una trasformazione significativa grazie alle tecnologie digitali e all'adozione di concetti chiave dell'Industria 4.0. Tecnologie come la sensoristica applicata alle macchine di produzione (e ai prodotti), la stampa additiva, la simulazione e prototipazione virtuale, i Big Data & Analytics e i Digital Twin stanno rivoluzionando le possibilità progettuali e offrendo vantaggi considerevoli alle imprese.
Con le tecnologie abilitanti dell’Industria 4.0, anche l’ufficio tecnico può fare affidamento su dati e informazioni rilevate dalla produzione che aiutano a migliorare la progettazione dei processi e dei prodotti, ottimizzando le prestazioni e aumentando il livello di sostenibilità. Il grande cambiamento, come ha spiegato Mario Guagliano professore ordinario del Politecnico di Milano nel suo keynote introduttivo, è l’interconnessione delle macchine che consente la raccolta di dati che, se opportunamente elaborati, possono supportare azioni correttive da implementare durante la fase produttiva, abilitare il concetto di manutenzione preventiva e ottimizzare la progettazione di processi e prodotti.
Molti i vantaggi per le imprese che intendono approcciare a questo percorso:
Miglioramento della progettazione: Le tecnologie digitali consentono agli uffici tecnici di raccogliere dati e informazioni rilevanti dalla produzione in tempo reale, che possono essere utilizzati per migliorare la progettazione dei processi e dei prodotti con una conseguente ottimizzazione della fase di progettazione e ingegnerizzazione.
Ottimizzazione delle prestazioni: l'analisi dei dati raccolti durante la fasi di produzione consente di identificare le aree di miglioramento e di ottimizzare le prestazioni dei processi e dei prodotti. Ciò può portare a una maggiore efficienza operativa e a una migliore qualità dei prodotti, oltre a una ottimizzazione (e quindi saving) delle materie, alla riduzione dei costi di produzione e dei costi associati alla gestione dei rifiuti e delle risorse, che tradotto significa un risparmio economico significativo per le imprese.
Aumento della sostenibilità: l'ottimizzazione dei processi descritti sopra, riducendo il consumo di energia e materie prime, contribuisce a ridurre l’impatto del processo di produzione e del prodotto stesso rendendoli più sostenibili. L'importanza dell'impatto sulle tematiche legate alla sostenibilità può crescere ulteriormente se durante la fase di progettazione viene considerata una priorità cruciale. La considerazione della sostenibilità durante la progettazione può stimolare l'innovazione e la differenziazione dei prodotti sul mercato. Le imprese che riescono a sviluppare soluzioni sostenibili e a comunicare in modo efficace i loro sforzi in questo ambito possono attrarre nuovi clienti e conquistare nuove opportunità di mercato, oltre che godere di una migliore reputazione presso i consumatori, i partner commerciali e la società in generale.
Le potenzialità del Digital Twin
Per i prossimi anni si prospetta un aumento del 30% di questa tecnologia, con un incremento della domanda di specialisti del 11% rispetto al 2021. Attualmente, quasi un terzo delle imprese negli Stati Uniti ha già adottato, in tutto o in parte, soluzioni basate sul concetto di Gemello Digitale.
Il Gemello Digitale consente di simulare e analizzare il comportamento dei processi (e dei prodotti) in diversi ambienti, utilizzando uno spazio virtuale dove è possibile modificare tutte le variabili. I principali vantaggi riscontrati dalle imprese che ne fanno già uso includono risparmi sui costi, progresso tecnologico, riduzione dei tempi di commercializzazione, introduzione di nuovi modelli di business, miglioramento delle capacità di personalizzazione, semplificazione dei flussi di lavoro e dei processi, e promozione di politiche di sostenibilità.
Migliorare il prodotto e servizio grazie ai dati raccolti sul campo: il caso Tecnoinox – Case study sviluppato con MADE Competence Center.
Nell'azienda Tecnoinox di Pordenone, specializzata nella produzione di cucine professionali per la ristorazione, l'impulso a progettare forni smart, intelligenti e connessi è stato fornito dall'ufficio marketing. Tale decisione è stata motivata dalla volontà di offrire nuovi servizi ai clienti finali. Dopo aver lanciato una prima linea di prodotti "alto di gamma", nel 2021 l'azienda ha optato per la realizzazione di una seconda linea smart destinata al mercato consumer.
Per la prima volta i progettisti dispongono di dati reali provenienti dall’effettivo utilizzo da parte dei consumatori e possono quindi apportare miglioramenti ai forni stessi grazie alle informazioni acquisite e non simulate.
Nel futuro l’azienda prevede di sensorizzare altri prodotti, con l'obiettivo di raccogliere su Cloud dati su cui continuare l’ottimizzazione dei prodotti e offrire nuovi servizi ad alto valore aggiunto ai clienti finali.
Prototipazione virtuale e Digital Twin: il caso MaCh3D
Con la simulazione e prototipazione virtuale, MaCh3D ha sviluppato un innovativo dinamometro per prove sui materiali, dimezzando i tempi di progettazione e minimizzando i costi di prototipazioni fisiche. L’idea nasce dall’esperienza maturata nel campo della simulazione ingegneristica applicata allo sviluppo prodotto e dal crescente bisogno di controllo qualità sulle performance meccaniche dei materiali, specialmente in settori come l’Additive Manufacturing o nei processi dell’economia circolare. Capace di erogare fino a 500 kg (5kN) di forza massima, concentrati in 15 kg di dispositivo, MaCh3D grazie alla progettazione virtuale è stata in grado di sviluppare uno strumento compatto e portatile che consente di testare i materiali non solo in laboratorio, ma direttamente nei reparti di produzione dei clienti. Inoltre, grazie agli strumenti digitali il prodotto è stato ottimizzato in tempi rapidi, senza bisogno di prototipazioni intermedie. La messa in produzione ha richiesto poi solo affinamenti ergonomici. Da poco disponibile sul mercato, presto sarà già disponibile un modello connettibile con la possibilità di sviluppare nuovi servizi basati sulla propria piattaforma Cloud. L’obiettivo è estrarre in tempo reale il set di informazioni necessari senza bisogno di ulteriori strumentazioni o tempi di attesa.
Democratizzazione dell’innovazione: il caso FloFleet
FloFleet è una start-up di giovani ingegneri dell'automazione e sviluppatori software che si distinguono per una forte propensione all'innovazione attraverso la collaborazione e la condivisione delle conoscenze. Essi hanno seguito un processo produttivo che ha sfruttato una combinazione di tecnologie digitali e conoscenze già disponibili, provenienti da vari settori. L'obiettivo primario è stato quello di sviluppare dirigibili elettrici e autonomi per il monitoraggio, le riprese aeree e la sorveglianza delle infrastrutture, superando i limiti di volo e di copertura dei droni tradizionali.
Per raggiungere questo obiettivo, FloFleet ha impiegato software di progettazione e simulazione virtuale, avvalendosi anche di risorse open source e moduli di Solidworks accessibili online. In fase di progettazione, sono stati acquisiti e utilizzati set di dati provenienti da ambiti apparentemente estranei al progetto, ma che si sono rivelati estremamente vantaggiosi per lo sviluppo del prodotto finale. Per esempio, dalle aziende produttrici di tendoni da circo sono state ottenute informazioni per la modellizzazione in 3D del tessuto del dirigibile; dai costruttori di piscine sono state ricavate indicazioni sulla saldatura del tessuto, e dai produttori di turbine sono stati ottenuti i disegni della struttura dell'attacco del motore.
Senza l'utilizzo delle tecnologie digitali per la simulazione e la modellazione, FloFleet non avrebbe potuto trasformare in informazioni i dati provenienti da altre industry e la realizzazione dei prototipi necessari per il passaggio alla fase di produzione sarebbe stata incomparabilmente più costosa. Il prodotto è in costante evoluzione grazie ai feedback del mercato.
Integrare i processi in chiave di sostenibilità: il caso Giacomini
Il processo di digitalizzazione in Giacomini è iniziato per esigenze di sostenibilità e circolarità, che richiedono e richiederanno sempre più la tracciabilità dei prodotti. L’azienda novarese è specializzata in lavorazioni meccaniche per il settore idro-termico, in particolare produce componentistica in leghe di ottone. Con 10 mila articoli, 23mila cicli di lavorazione e quarant’anni di attività, era una azienda gestita “a silos” tramite fogli Excel. L’aumento della complessità, con nuove leghe metalliche e la necessità di tracciare materiali e prodotti, ha imposto la recente introduzione di software e sensori nella produzione. L’obiettivo che l’azienda si è posta è di arrivare a una gestione integrata di tutte le fasi produttive. Cicli di lavoro, modellazione 3D, controlli qualitativi a fine linea saranno collegati tra loro, con flussi di informazioni disponibili e confrontabili tra loro. Questo cambiamento gestionale impatta anche sull’organizzazione: i colleghi stanno imparando a lavorare in team e a sfruttare le informazioni per ottimizzare processi e prodotti. Il progettista stesso assume un ruolo nuovo: non più solo disegnatore, ma detentore di know-how aziendale da utilizzare in fase progettuale.