Manutenzione smart grazie a big data e machine learning
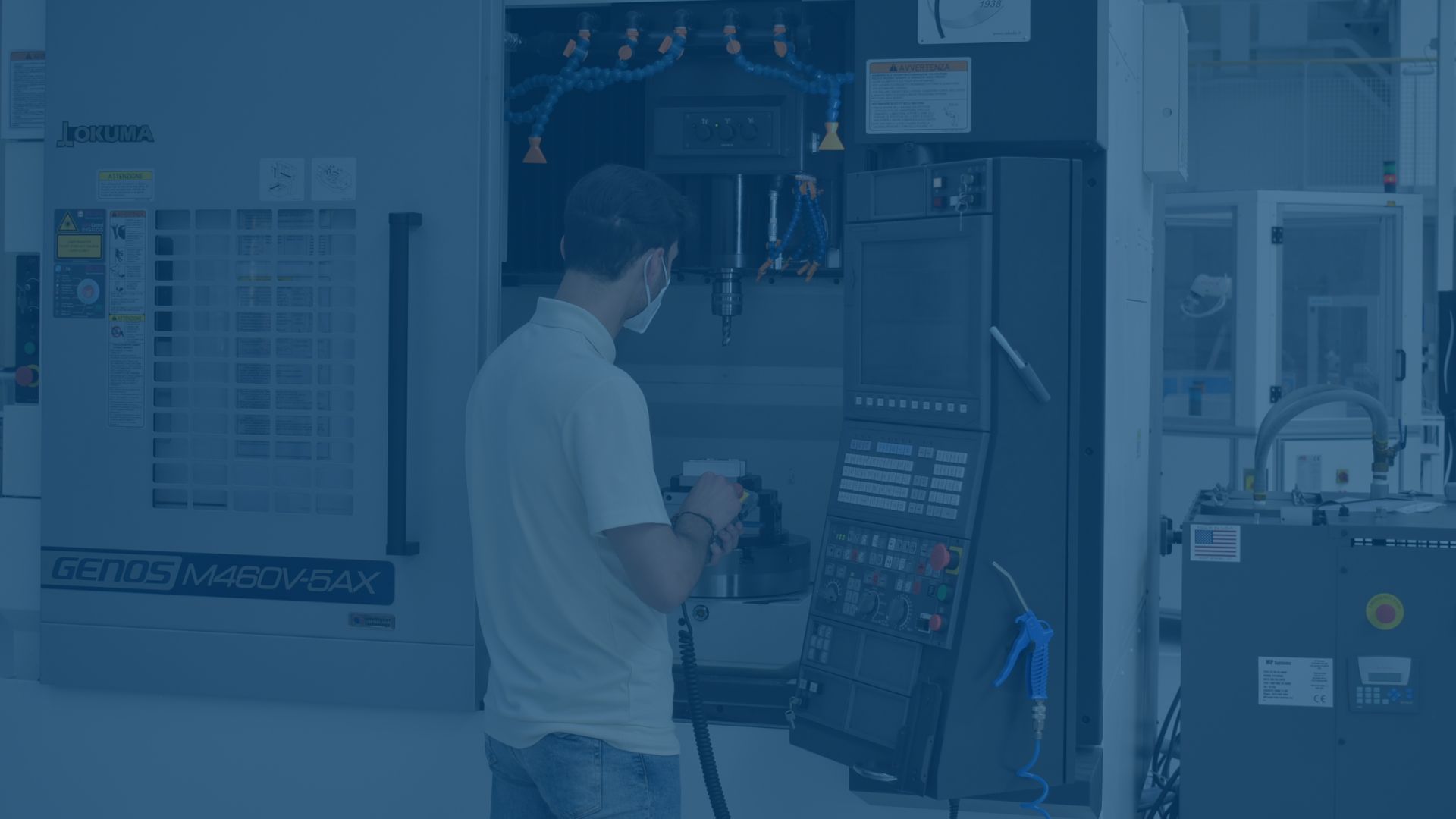
I vantaggi della manutenzione predittiva al centro dell’aperitivo tecnologico organizzato da MADE4.0, in collaborazione con Tecniche Nuove Media. L’impatto dell’AI e del machine learning sulla manutenzione industriale, con la testimonianza di Cosberg e Progeo Molini e l’esperienza di Iacchetti Ingegneria.
Manutenzione correttiva, manutenzione preventiva e manutenzione predittiva: un cambio di paradigma grazie alle tecnologie IoT, big data e machine learning. L’utilizzo di modelli predittivi di intelligenza artificiale per gestire la manutenzione degli impianti industriali richiede standardizzazione dei processi e monitoraggio dei comportamenti delle macchine, con un forte impatto sui costi variabili di processo. Ora è possibile ridurre le ore del fermo macchina per guasti improvvisi e risparmiare sui cicli di manutenzione preventiva che, in assenza di un’accurata analisi dei rischi, rischiano di essere ridondanti e non necessari. Prevedere un guasto per tempo e pianificare in modo funzionale gli interventi di manutenzione significa anche essere in grado di gestire al meglio la Supply Chain, con un approvvigionamento tempestivo dei pezzi di ricambio e l’intervento puntuale del service di manutenzione.
La manutenzione predittiva è un progetto multidisciplinare
La manutenzione Smart (Smart Maintenance) non è solo una questione di tecnologie, ma coinvolge fin dall’inizio organizzazione e strategia. Come ha spiegato nel keynote introduttivo Mauro Macchi, professore di ingegneria industriale al Politecnico di Milano, la scelta dev’essere “on purpose”, cioè bisogna decidere su quali asset critici intervenire con la sensorizzazione (IoT), perché e per quali obiettivi. Bisogna quindi lavorare sui dati per uniformarli, pulirli e utilizzare solo quelli che effettivamente servono allo scopo, con skill digitali e di data analytics. Ma bisogna anche avvalersi sempre di competenze ingegneristiche di processo e manutentive per fornire al modello da addestrare (machine learning) informazioni corrette e complete rispetto ai comportamenti delle macchine, alle anomalie e alle ricorrenze di causa-effetto per una corretta analisi dei rischi (prognosi).
La manutenzione predittiva è dunque il risultato della collaborazione di team multidisciplinari, che coinvolgono esperti di dominio di produzione, manutenzione, automazione e analisi dei dati. La raccomandazione emersa dall’aperitivo tecnologico “Machine Learning e Big Data per la manutenzione predittiva: opportunità e vincoli” è dunque di calibrare e integrare tra loro tecniche sia manutentive sia di Intelligenza artificiale, in base agli obiettivi da raggiungere e al dimensionamento del progetto, senza mai perdere di vista la leva organizzativa. MADE4.0 supporta le Pmi nell’implementazione di tecnologie 4.0 (Iot, big data analytics e machine learning) per la manutenzione predittiva, mettendo a disposizione delle imprese competenze tecnologiche, ingegneristiche e digitali.
I vantaggi del machine learning per la manutenzione predittiva
I vantaggi operativi della manutenzione predittiva sono:
- Riduzione dei tempi di inattività per guasti improvvisi, anticipando i rischi e rendendo più efficiente la produzione.
- Riduzione di rischi dagli impatti severi, in termini di sicurezza, qualità e ambiente.
- Una manutenzione più efficiente, perché possono venire pianificati interventi tempestivi, ma solo quando servono davvero, grazie alle raccomandazioni di un sistema intelligente, alimentato costantemente dai dati di produzione e con supervisione dell’ingegnere di manutenzione.
- Standardizzazione di un processo di gestione con monitoraggio costante del funzionamento delle macchine fino all’intervento manutentivo (IoT + AI + machine learning).
- Upskilling del personale di manutenzione: più cultura del dato e rispetto delle procedure di manutenzione.
Primo passo, quali asset sensorizzare? L’esperienza Iacchetti e la collaborazione con MADE4.0
La società di ingegneria elettronica di Crema Iacchetti è stata coinvolta in un intervento di sensorizzazione degli impianti per la manutenzione di ascensori e scale mobili gestiti da un gruppo industriale. Per la raccolta dati sullo stato di funzionamento degli impianti è stata utilizzata la tecnologia IoT, ma con due complessità da gestire: mezzi piuttosto datati e provenienti da differenti produttori. Il primo passo necessario è stato reperire le informazioni tecniche di ogni mezzo (300 scale mobili e 100 ascensori), quindi, grazie a un confronto con i manutentori, sono stati individuati i parametri funzionali alla manutenzione (vibrazioni, movimenti delle porte, trazione e usura corrimani) da monitorare. Data la complessità dell’intervento si è reso addirittura necessario sviluppare nuovi sensori.
Nello specifico, con il supporto di MADE4.0, è stato ingegnerizzato un sensore ottico per rilevare l’usura dei corrimano attraverso le anomalie nel colore. Oggi i dati sono raccolti e integrati in una piattaforma web, nella quale il committente potrà avere tutti i dati disponibili abilitando il concetto di manutenzione preventiva. (analisi dei rischi e Smart Maintenance).
Un sensore di origine militare per la manutenzione predittiva - il caso Progeo Molini
Come sappiamo le tecnologie digitali sono trasversali ai settori industriali e possono trovare applicazioni anche all’esterno del mondo manifatturiero concepito in senso stretto. Il produttore modenese di mangimi Progeo Molini, per esempio, negli ultimi 30 mesi, ha rivoluzionato il proprio approccio alla manutenzione, aumentando del 25% la produzione, risparmiando 60 ore di fermo impianti grazie ai nuovi programmi di manutenzione. Il cambiamento è stato sistemico ed ha avuto origine dal Controllo di Supervisione e Acquisizione Dati (una categoria di applicazioni software per il controllo dei processi industriali, in inglese Supervisory Control And Data Acquisition – SCADA ndr) sul funzionamento dei 1.575 asset aziendali. Da questo processo è stata realizzata una mappatura completa delle macchine e di tutte le cause dei guasti registrate. Coinvolgendo i reparti produzione, manutenzione, automazione e IT, è stato possibile introdurre innovazione passando da una manutenzione classica, ovvero al manifestarsi del guasto (correttiva) a una manutenzione ‘smart’, calibrando le diverse tecniche di manutenzione in base alle priorità produttive e soprattutto grazie alla comprensione delle cause dei guasti. Alcuni asset focali sono stati sensorizzati e vengono monitorati per abilitare manutenzione predittiva. A regime, questa metodologia verrà applicata al 40% degli impianti. Nel progetto è stato utilizzato per la prima volta, in ambito civile, un sensore di origine militare, che grazie all’edge computing consente di rilevare ed elaborare già a bordo macchina temperatura e pressione, senza utilizzo del Cloud.
Come spesso accade, i progetti di innovazione tecnologica abilitano anche i concetti di sostenibilità. Grazie all’ottimizzazione della manutenzione e quindi a un migliore stato di salute delle macchine, i consumi energetici sono calati del -12%, mentre i decibel acustici prodotti dagli attriti delle macchine sono scesi mediamente di 9 decibel.
I vantaggi commerciali della servitizzazione - il caso Cosberg
Cosberg, azienda bergamasca specializzata nella progettazione e costruzione di macchine per l'automazione dei processi di montaggio, già da qualche tempo propone un servizio di manutenzione predittiva sui componenti, individuati come più critici, dei moduli che compongono la macchina e la linea di produzione, affidando a tecnologie di machine learning, opportunamente addestrate, l’analisi del rischio di funzioni. L’obiettivo è essere in grado di programmare e procedere con l’intervento manutentivo prima che il guasto si verifichi con un evidente risparmio dei costi variabili (legati ai servizi di manutenzione), e massimizzando il rendimento del processo produttivo, (si eliminano i tempi di inattività della macchina). I dati a disposizione di Cosberg dicono che i loro clienti che hanno adottato questo servizio hanno ridotto inefficienze tra il 2 e il 4%, misurate dall’OEE (Overall Equipment Effectiveness), che misura la produttività delle apparecchiature aziendali non solo in base alla prestazione (efficienza rispetto alla velocità massima potenziale), ma anche dalla disponibilità (la quantità di tempo in cui sono in funzione rispetto al tempo totale di funzionamento previsto) e alla qualità (numero di prodotti realizzati che soddisfano gli standard di qualità stabiliti). I vantaggi del machine learning sulla gestione predittiva dei guasti diventa quindi una leva commerciale competitiva per i produttori di macchine. Cosberg nei suoi investimenti continui in ricerca e innovazione collabora attivamente con l’ecosistema, per avvantaggiarsi delle competenze che non può avere internamente, come nel caso dei numerosi progetti sviluppati con MADE4.0.